THE COST OF RACING: IMPROVED PRODUCTION
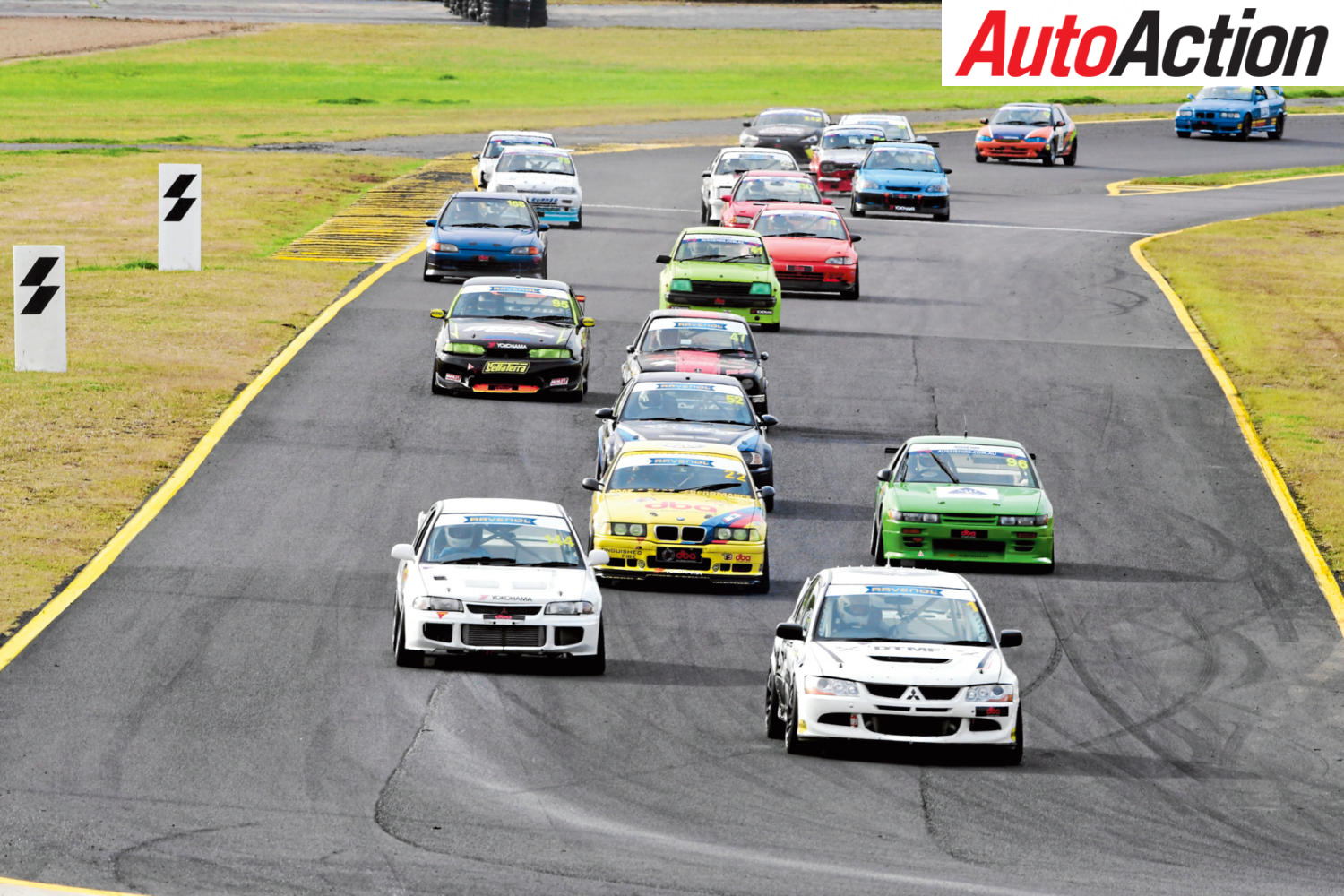
Improved Production features the broadest eligibility list in the country, yet the regulations have been stable for 40 years. The attractiveness of this class is that it caters for a wide variety of competitors, as Heath McAlpine discovered.
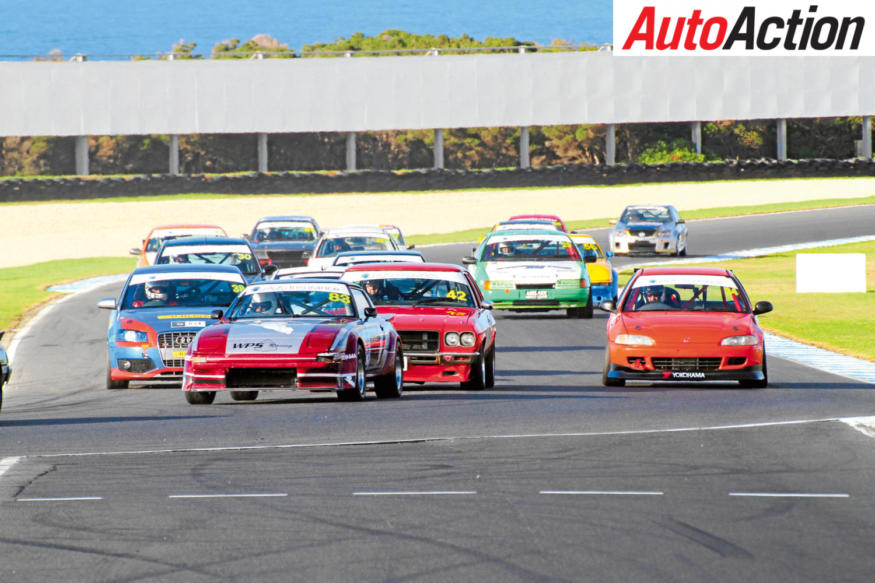
Cost of Racing: Improved Production
There is a broad appeal on offer when it comes to Improved Production, as the category provides an eclectic mix of makes and models mildly modified for racing application.
It rewards different strengths, can be entered on a tight budget where development is progressive, however one underlying fact remains which is that car choice is key to either an expensive or inexpensive build.
Split into two divisions – Under and Over 2-Litre – Improved Production is one of the only classes to be raced in each state, plus the Northern Territory.
The Improved Production Nationals attracts more than 150 entries depending on the circuit.
The Victorian Improved Production Championship is one of the most populous, with in excess of 40 entries at every round, making it very competitive.
President Gary McKay is a competitor racing his pride and joy, a Holden LJ Torana GTR XU-1, which was in fact his first road car.
He explained to Auto Action that the stability in the Improved Production regulations is particularly advantageous to grassroots competitors because car construction can take years rather than months.
“The strongest part of our category is the fact (that) rules haven’t changed in many, many years, so as much as you can buy a car of the lot and race it, some competitors take three or four years to build (one),” McKay said.
“Being a grassroots motorsport, 99 per cent of the competitors are normal people with normal wages, who don’t have bucketloads of money to spend, hence it takes quite some years to build these cars. So, the good news is that when they start building the car, they know that in two, three years’ time, it’s still eligible because the ruleset hasn’t changed.
“For me, as far as cost is concerned, you can physically buy a second-hand car, chuck a seat in, chuck a cage in and do all the (other) safety features, and basically run as stock standard if you want. Or you can go right through to literally spending hundreds of thousands of dollars, if you want to go down that avenue.”
McKay’s view is that an Improved Production car could be built for under $20,000, but don’t expect it to be a frontrunner at that price.
As much as it is about dollars, it is also about choosing the right base package, which is the tipping point between an inexpensive or costly build.
“Probably towards the back end, it won’t be slowest,” McKay said of a $20,000 build.
“I mean, you wouldn’t want to go and buy a slow car. I mean no disrespect but you wouldn’t want to buy an Excel and expect to be a mid-runner.
“If you want to spend $40,000 or something along those figures, you could buy yourself a VE Commodore because these days the its quite an old car.”
While Victoria features a strong Over 2-Litre field, up north in New South Wales, a strong field of smaller capacity machinery appears at Sydney Motorsport Park and Wakefield Park.
NSW Improved Production vice president Joseph Lenthall shared McKay’s view that cost and competitiveness is up to the base make and model that is selected.
“You can run at that entry-level across most cars for a long period of time. Anything from a VK Commodore to a VF Commodore, a late model BMW to an E30 or any kind of S-chassis Nissan or Evo,” Lenthall said.
“You can do this with a wide variety of cars and the difference is with our category compared to others you can get on track reasonably inexpensively and if a good choice of car is made, it can be competitive at a frugal cost.
“If you choose, for instance, an Evo, you know is it going to be a fast car.”
Improved Production racing is accessible through the used car market, with a top NSW Nissan S15 Silvia being advertised for $40,000.
Whereas, building a new car can be very expensive, especially if outsourced through components like labour, engineering, wiring and paint.
A new entrant to the NSW field has chosen an obscure but competitive model that is a perfect example of an affordable build.
The Honda Accord Euro built and driven by Justin McMahon is one of the newest entries on the grid, and features many factory parts including the engine, gearbox, while the brakes have been uprated and the roll cage self-built.
Luke Grech-Cumbo knows how to run up the pointy end. He is a multiple Victorian Improved Production champion driving his familiar green HSV Senator. The beast was his first try at car construction built with the motto “Do it twice, make it nice” and so far, it has delivered him great success.
Built in his shed alongside another Improved Production entry in the form of Ian McLennan’s Holden Monaro, Grech-Cumbo believes with labour costs added, the Senator build would have set him back $100,000.
But with the experience under his belt, he believes that the repeatable cost to build a similar car could be half that.
“If you wanted to build a car like mine, knowing what I know now and without the Holinger gearbox, you could probably do it for $50,000,” Grech-Cumbo told Auto Action.
That would provide a good base, but to take the next step up in competitiveness, further investment would be required.
“If you want those extra tenths you need better suspension, a Holinger, lightweight flywheel, so to build a car that is capable of winning you need around $80,000,” he added.
The starting point of Grech-Cumbo’s racer was an already caged VX Commodore shell, bought for $4000, which was regulations compliant. An LS1 engine, T56 gearbox, factory computer and wet sump was installed, with the driveline owing Grech-Cumbo $6000. However, oiil surge was problematic, forcing him to take the next step.
“This consisted of a 6.0-litre LS motor with an aftermarket cam and dry sump, which then needed a new tank, plumbing, coolers and filter adaptors, bumping the cost out to $10,000.”
As the stresses on engine components increased due to the Senator going ever faster, further advancements are currently being planned by Grech-Cumbo as he builds a new engine.
“For the first two years I ran a factory crank, but when we started turning it up, we put a stronger steel one,” Grech-Cumbo told Auto Action. “It runs forged rods and pistons with factory lifters and rockers. That’s something on the next engine we’re going to get a bit more serious (about) because all but one of my engine failures have been valve or valve train related.”
This raises the price of the engine to approximately $20,000, and for that the end product produces close to the same amount of horsepower as a Supercar. Yet, it still runs a factory ECU.
The aim for the Senator is to make it the best all-round package, so Grech-Cumbo has budgeted in areas including the suspension, where the current system is worth $8,000.
“I’ve got Harrop uprights to try and get rid of bump steer in the front, but to get started you don’t need that,” he emphasised. “My original set of coil overs cost me $3500 and they were good. I ran them until mid-2018. However, when I bolted the Harrop ones on, I didn’t change a thing and went 1.4s quicker.”
Grech-Cumbo also noted that shock packages such as the XYZ which be bought for $990 are also suitable and competitive, which is what McLennan runs in his Monaro.
With the Senator being so powerful but so heavy, big brakes are important with Grech-Cumbo utilising a similar Alcon system to that used by V8 Supercars in 2005 which feature six-pot calipers on the front and 4-pot on the rear, costing $6,000 a set. A recent change to Forza rotors has been beneficial to longevity with a set now lasting a season.
Driveline is another area where the Senator has been further developed. A Holinger H6S is Grech-Cumbo’s gearbox of choice, costing around $12,000 on the second-hand market, while another popular option is the RD6, which new costs $18,000.
A Tilton triple-plate clutch was installed at the cost of $2500, aiding performance and in servicing as any part can be replaced, unlike its factory counterpart.
An array of MoTeC hardware is at Grech-Cumbo’s disposal in the Senator at a cost of between $5000-$6000
“I’m a big believer in data. I’m not Jamie Whincup but I definitely find using data is helpful,” Grech Cumbo said. “That’s optional though.
“I don’t use shock pots. I’ve got all the engine data, plus brake sensors, throttle tracers and longitudinal g-force. I use the engine data a lot for maintenance and looking after it. Temperatures are something that is really important, especially in Commodores, I mean I welded the diff up at Bathurst because it was so hot!”
A Velo race seat was purchased for $800 and a wheel for $300, but the latter can remain as it left the factory if competitors wish. A fire bomb was also installed for $800-$900, though a $40 extinguisher will suffice.
“I have a fire bomb in mine, I bought it with the idea of protecting the investment rather than me,” Grech-Cumbo explained. “It’s an expensive car to burn to the ground.”
The Senator doesn’t contain a radio, just GoPros which can relay information back to Grech-Cumbo and engineer Rick Kemp at Race Technique Engineering, who attends the track one day a year at a cost of between $500-$1000. Despite that, the two are in constant dialogue even when Kemp is absent.
Grech-Cumbo’s budget works out to be $3000 a meeting including the $600 entry fee, $300 of United E85 Fuel, plus general wear and tear on the Senator. The Yokohama AO50 last a year, though he also runs sprints outside of Improved Production duties. For interstate meetings, the budget extends to $5000 including accommodation and all the extras necessary to compete.
Regular meeting costs include changing the oil and filter after each using high-grade racing oil at $200.
In the 2-Litre class, current TCR Australia driver Jordan Cox plied his trade and caused a stir during the 2017 Bathurst support race, in a Honda Civic.
Since then the Honda has been sold and his latest project is a Suzuki Swift, which he started his career in. Cox’s build is typical of the more affordable end of the spectrum.
A roll cage was installed along with a seat and belts, both of which came free. The MOMO steering wheel came with the purchase of the Swift and a $40 fire extinguisher was installed.
The Swift also came with a set of Koni Sports shock absorbers, then Cox put a set of brake pads in it, welded the diff and built an exhaust, before the Suzuki hit the track.
Updates to the suspension cost $5000 – $7000 when things got serious, Cox designing his own suspension and calling on an engineer to help out.
“I ran it for a few years with stock suspension and the Koni shocks,” Cox explained.
“I got introduced to an engineer in Nowra, who made up what I drew in terms of pick up points, to lower the car to the 100mm ride height rules. Then we changed the roll centre, fitted aero-grade tierods and bearings, I found a different upright off another model Suzuki that had better stiffness and geometry.
“Although these didn’t make the car a whole lot quicker, it was nicer to drive, better on its tyres and easier to make set-up changes.
“The engine is probably my proudest part of the car,” Cox said.
“It’s the simplest and cheapest part of the car. With a turbo you don’t have to spend a lot of money on the engine internals to make the power, it’s the bolt on parts that are expensive, probably worth $15,000.
“The engine is a standard 1.3-litre head with a set of cams. I got a 1.6-litre block from a later model Suzuki for the twin cam head, because it’s a bolt on fit. We run standard cast pistons, put a set of rings and bearings in it, I upgraded the rods at $500, so the start-up cost of the engine was probably $2,500 to build up parts and labour, though I did it myself. So you’d add another $3,000 if an engine builder is used.”
The Swift has a WRC rally-spec turbo with standard non-light bits retained, while the fabricated intake manifold, exhaust and internal wastegate is where the expense of the bolt ons emerges.
“The biggest cost with the Suzuki was everything had to be custom made, there’s nothing that can be bought and bolted straight on,” Cox reflected.
Electronics is one of the areas that Cox has spent money as the software needed to control the engine has to be accurate and reliable. In the Swift’s case, a MoTeC M1 ECU is wired to a CDL3 display and E888 expander, costing $10,000 including labour and sensors.
Depending on the situation, tyres last two race meetings but if it was an important event, Cox will chuck two new front tyres on, while rears generally last a season.
“Yokohama AO50 is probably one of the most expensive semi-slicks out there, but you get bang for your buck, I think it’s the best until they’re worn,” he said.
Brakes were acquired from the Honda with Spoon 4-pot calipers on the front and Wilwood 2-pots on the rear. Hubs and adapters needed to be machined, plus a set of rotors which cost $150 and last a season and a half. An adjustable pedal box comes to $5,000.
Circo Pads at a cost of $350 last four meetings in the front and a whole season at the rear.
Mates help Cox out at race meetings, so while Go Pros are in the car for the ‘online social media crew’, a radio is not.
Cox budgets around $1,000-$1,500 for each state meeting.
He emphasised that putting money in the right areas will provide a better outcome at the end of the day.
“I’ve always been pretty budget conscious with the development and modifications I’ve done to the car. Any money has always been spent on areas of the car that provide performance,” Cox concluded.
The figures that both Grech-Cumbo and Cox outlined to Auto Action are to run well, competitively, within their respective budgets.
In Improved production what decides the budget is the vehicle, class and level the competitor chooses to participate in.
And that’s what makes Improved Production so accessible.
COST GUIDE
New car build – $20,000-$100,000 plus
Used Car – $15,000-$60,000 plus
Meeting costs -$2500 (state round including consumables, fees, transport), $6000 (large interstate meeting)
Tyres – Yokohama AO50 control tyre $1800-$2000 a set (depending on size)
Entry fees
$395-$600 (state level round),
$2000 (major interstate meetings)
ABOUT IMPROVED PRODUCTION
Regulations for Improved Production are open to an extent, but tightly controlled.
They also divide eligible cars into Pre-1986 and Post-1986, a differentiator which was established some years ago to increase the number of newer models in the class, which saw some concessions made to these.
An engine must use a block from the same manufacturer’s family, not be motorsport specific, be a maximum of 6-litres and feature the same rotors or pistons as the road-going example. However, engine internals and exhaust are free, while Turbos are restricted based on a model’s weight.
Clutch, flywheel and transmissions are free, for example, Holinger’s array of H-pattern gearboxes are popular, however paddle-shift and sequential are outlawed unless the model comes that way from the factory with a DSG or DCT transmission.
Pick up points cannot be changed in terms of suspension, lower control arms and tie rods must be identical to factory specification, which takes away the possibility of intricate Sports Sedan style systems.
Brakes are free, though restricted by wheel size, which is dictated by a chart within the Improved Production regulations based on the type of car, weight and engine.
ECUs are free too, though traction control is not allowed and ABS can only be run if done so through a factory unit.
Yokohama is the control tyre supplier for Improved Production across Australia with its AO50 semi-slick.
Aero is almost non-existent, though a category-specific adjustable rear-wing can be installed on the newer models, while flares can be fitted on the Pre-1986 models.
Rollcage and safety equipment is standardised as per the Motorsport Australia rules.