WHAT’S IN THE WORKSHOP – BENDIGO RETRO MUSCLE CARS
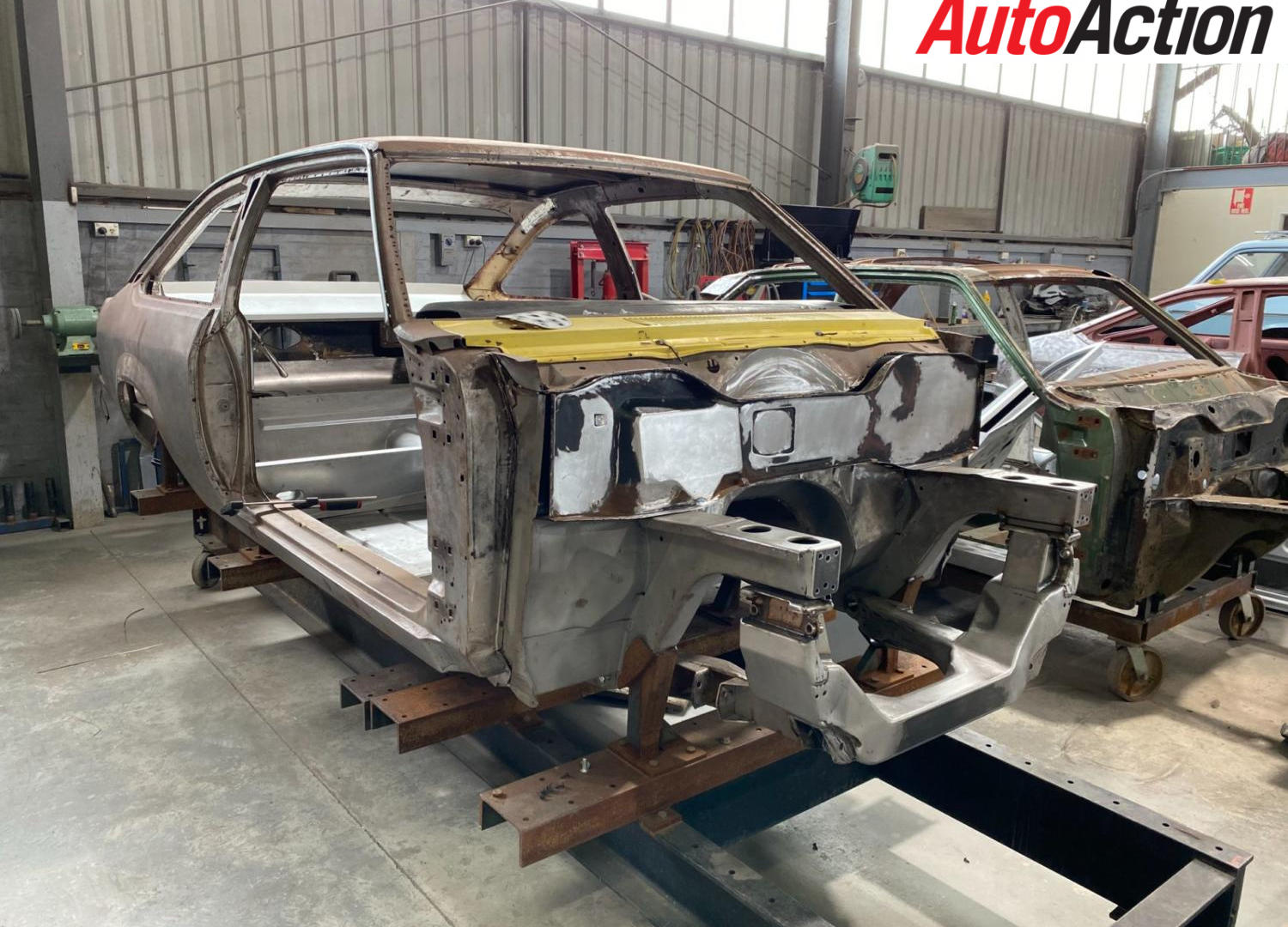
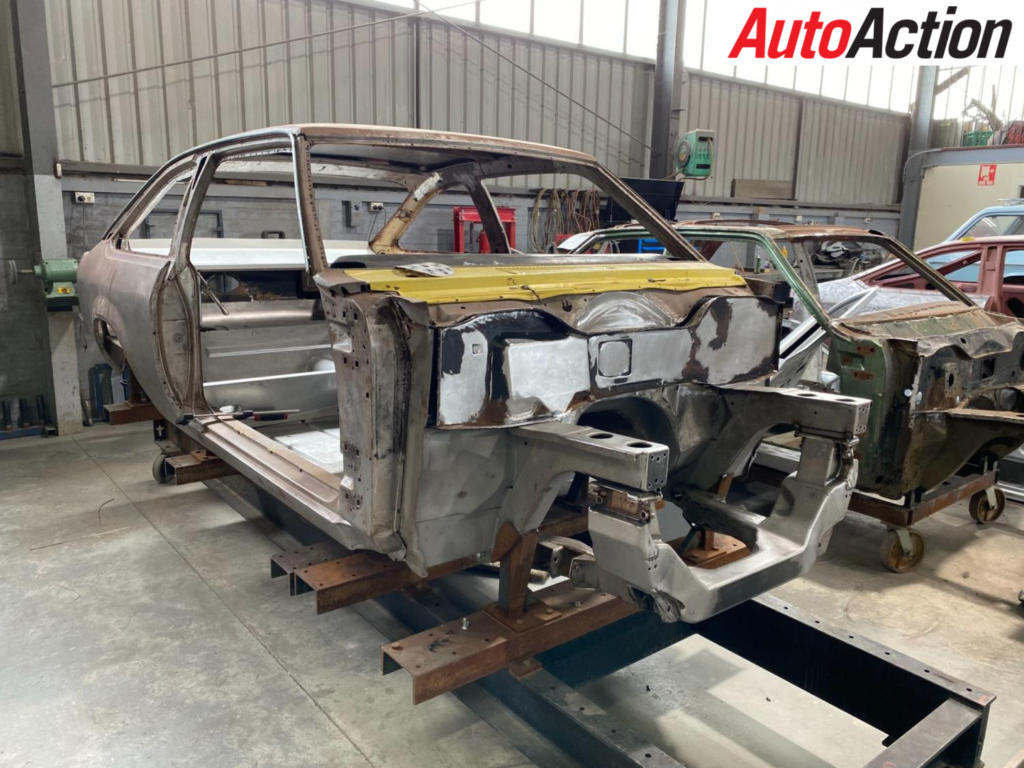
What’s in the Workshop – Bendigo Retro Muscle Cars
Work has never stopped during the various Victorian lockdowns for Gary O’Brien and the Bendigo Retro Muscle Cars crew as it builds the next generation of Touring Car Masters machinery.
By HEATH McALPINE
Among the projects at its rural Victorian base are a new VC Commodore, an HQ and a Torana Hatchback.
“We’re on the home straight on the VC Commodore, I’m hoping to have that done by the end of the year,” O’Brien told Auto Action.
Testing is planned for the newest addition to the TCM grid in January, but plenty of work has gone into making the next-generation of models easier and cheaper to repair.
“We’ve done a lot of R&D because what I’m trying to do with all the TCM Toranas and Commodores is to build crash systems into them by making the fronts of each very modular and the rears modular,” O’Brien explained.
“When the car gets a fair old whack in the front, it might be a dozen bolts and a few wiggies before you pull the whole front off it, then you can put new rail extensions, radiator support to have those all sub-assembled.
“From my perspective – being a crash guy – you’ve got to make it easier to work on them at the track.”
The HQ build promises to be one of, if not the best builds on the grid and again this is due to the innovation displayed.
“What we’ve done with a customer’s HQ, which is a really high-end build like a Supercar through the workmanship, it’s a step up from the Torana,” O’Brien said.
“It’s got rail extensions, they’re factory rails, but we’ve sliced and diced them and they bolt on. You could have a radiator support nosecone with a set of rails and instead of putting on racks or jigs, the way they’re all braced up to the wishbones and main crossmembers are, the fronts you just throw away.
Not only are the current builds cheaper and easier to repair, but safety is increased as well.
“In the rear of the HQ we’ve made it all modular with the back panels, we’ve made composites of coupe quarter panels you see for sale second hand at $8000,” explained O’Brien. “We’ve taken the position to do composites stuff so they are glued and pop-riveted on. The back panels we’ve done the same.
“We’ve got a little crash area in the back of it, a nice beam and a bit more safety around the fuel cell. Originally, you’d need edging and cut a hole in the boot floor with a piece of square tube there.”
To highlight the exceptional quality of the HQ, which also features a 350 Chev with more than 700hp and a G-Force gearbox, O’Brien is proud to describe the construction nuances.
“On this HQ, the frame of this car, it could go down the road without sheet metal work,” he said. “The floorpan is a structure, but basically the sheet metal and the roof just keeps the water off you. The sides are all detachable, again thinking off of crashing it, they all bolt to a framework inside. When you look at it from the outside, it still looks standard so it’s not radical chopping and channelling. There’s been a fair bit of thought has gone into how to mount the chassis onto it and how to keep the sides safe in the case of a side impact.”
The Hatchback is an evolution of John Bowe’s all-conquering Torana, but will feature mostly Australian-sourced parts, an achievement O’Brien is only glad to disclose.
As racing gets back underway, What’s In The Workshop will continue albeit in a staggered manner.
For more of the latest motorsport news pick up the current issue of Auto Action. Also make sure you follow us on social media Facebook, Twitter, Instagram or our weekly email newsletter for all the latest updates between issues.