UNDER THE SKIN: HOLDEN VY SUPERCAR PE041 – FIRST AND LAST
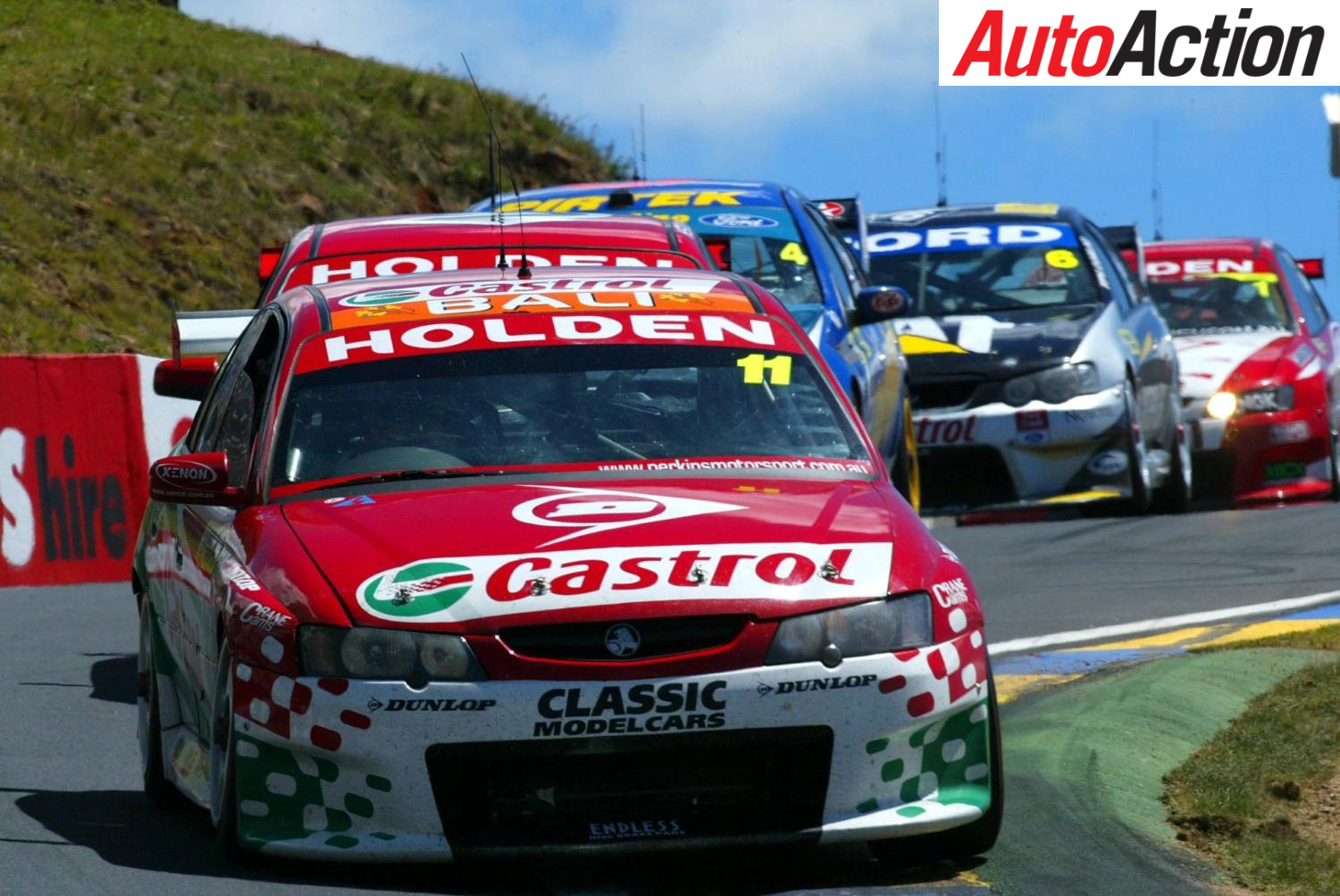
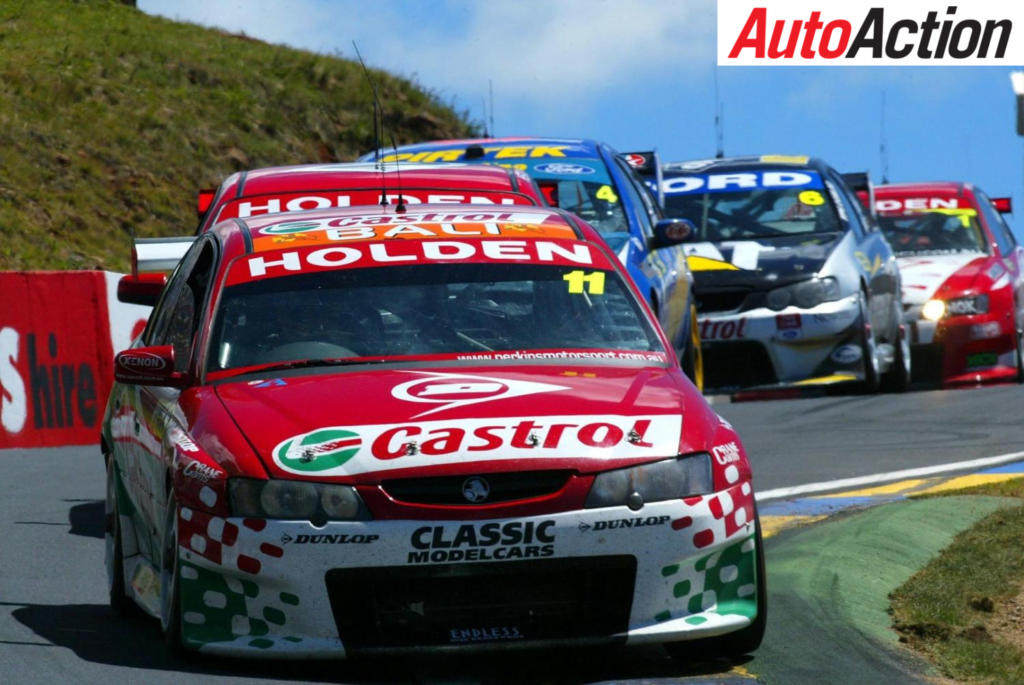
Under The Skin: Holden VY Commodore Supercar – PE041
Perkins Engineering chassis PE041 is significant in more than one way — it is the first Project Blueprint Commodore built by the team, the first to predominantly use CAD design, the final Bathurst entry for Larry Perkins, the first for his son Jack — and the only car that the team ever kept.
By HEATH McALPINE
The Castrol Commodore has been accurately restored by Jack to the exact specifications it ran with at the 2003 Bathurst 1000.
The lead-up to that race involved an all-nighter to repair the car after it was severely damaged at The Cutting.
Since that event, the Commodore has been driven by the likes of former Perkins alumni Steve Richards, Paul Dumbrell, Alex Davison and Shane Price. It has also been painted in the colours of Castrol, Autobarn, Jack Daniels and, obscurely, Sirromet Wines in a history spanning four years.
When the Kellys bought Perkins Engineering at the end of 2008, the car, though still owned by Perkins, was moved into the new workshop with the idea of it being restored to its former glory. But because of the pressure of getting four entries ready for the coming V8 Supercars season, it failed to happen.
Since then it has been a side project for the younger Perkins, and as a restoration project it is now identical to the Commodore that took the grid on October 12, 2003.
“It certainly was the last car that I drove at Bathurst and that was my last race,” said Larry Perkins.
“On the other side of the coin it was probably the car that I did the least hands-on work because I had about 60 people working for me. Twenty years ago I was hands-on, but I had a lot of good guys around me and they put all this together.
“I was just the driver.”
After it was built in June 2003, Steve Richards gave the car its debut at Hidden Valley, where its best finish was fifth in the final race. The first VY constructed by Perkins Engineering was the first built under Project Blueprint, which was designed to equalise the V8 Supercars field at the time.
Project Blueprint introduced common suspension pick-up points and in particular saw both Holden and Ford-based cars run a double wishbone coil-over front suspension.
The chassis pick-up points, the wheelbase and track were all mandated as well as driving position and aerodynamic changes, all meant to stop the parity debate that had been sparked by the dominance of the Holden Racing Team.
Richards and Perkins shared the car during the Sandown 500, where they finished sixth before the annual pilgrimage to Bathurst, which began in great fashion when the Commodore qualified for the Top 10 Shootout. The weekend turned sour, however, as Perkins recounted to Auto Action.
“It was to do with V8 Supercars and CAMS somehow getting together and you had to sign a letter of indemnity that covered both for negligence and I refused to sign it,” Perkins said.
“I’m not covering anyone for negligence.
“My team manager was on the radio during the last practice session saying, ‘You’ve got to come in, they’re going to black flag you,’ and I’m saying to him, ‘Tell them to eh, eh, eh, eh.’
“I’ve arrived at this turn (The Cutting) nearly 20kmh faster than I should have been, which is a huge error and promptly ploughed it into the fence. It took 15 inches (38cm) out of the front and nearly pulled all my gizzards out.”
The incident occurred in the final practice session on Saturday, which meant the Perkins Engineering crew worked through the night to repair the Commodore. This was completed successfully to standards Perkins recalls were “superb … I couldn’t tell it from before the crash”.
That was proved to be the case at the end of 161 laps around Bathurst where Richards and Perkins finished the day just shy of the podium in fourth. The Commodore then finished the season with Richards before starting the 2004 championship in his hands, then the chassis was driven by Alex Davison in the series finale.
The Commodore was then repainted in Autobarn colours for Davison to race in 2005, though he was dropped in favour of Owen Kelly for the final two rounds. It became a spare car in 2006, just as Jack Daniel’s became naming rights sponsor and it was sent to the Ohlins Shock Absorbers subsidiary sales and distribution centre in North Carolina for testing on its shaker rig. This makes this chassis one of the few V8 Supercars to not only go to the US, but test at Ohlins.
This Commodore was brought into service for the endurance events for Development Series drivers Shane Price and his son Jack, who finished 24th at Sandown, then Bathurst where it was disaster on the first lap, as the younger Perkins tells it.
“It’s the car that I took out Mark Skaife — or he took me out, I still think — at Bathurst 2006,” he said. “There was a lot of damage to the left-hand side and our first crack at Bathurst was done in only a few seconds.”
The car was then repaired for Dumbrell to race on the Gold Coast before being re-liveried to Sirromet Wines colours to fulfill Nemo Racing’s licence requirements after Paul Radisich’s big Bathurst crash in 2006.
Phillip Island 2006, with Price behind the wheel, was the last time it raced.
The younger Perkins has completed a ground-up restoration of the Commodore, so accurate that it carries the majority of the same components it did when gridded up for the Bathurst 1000 17 years ago.
A point of difference between this Commodore and other VYs running at the time was that this was a full-Project Blueprint build. Because of the brief turnaround, many teams converted VXs into the new model, which meant most still retained the Chevrolet 18-degree motor — this did not.
Fitted with the then-new Holden Motorsport “Aurora” engine, a lot of work went into searching and finding the very same components that were fitted into the car when it took to the grid at Bathurst.
“We did have everything around the workshop and I was able to get it all back together, including the fundamental parts of the engine,” Perkins said.
“It is (Perkins Engineering) engine 184, cylinder heads are set 52. They were still in circulation so we were able to put them back on the engine and marry that all back up.
“We’ve got the original rocker covers from the 2003 meeting and basically everything under the bonnet is original parts from when the car ran back then. Even the water flow bottle, power steering reservoir bottle, all other items were as original as we could find.”
Because of the development of the engine during its initial run, the airbox had many iterations, making it hard to piece the item together.
“Finding all the original airbox pieces wasn’t easy,” he said. “It was such a period of evolution with the brand-new Holden Motorsport engine that there were five or six versions of this airbox. It matches the radiator ducts, the radiator and the manifold, just to name a few.”
The engine was rebuilt to 2003 specifications right down to the manifold, trumpets and fuel rail injections, ensuring the mechanicals are accurate.
A Holinger H-pattern gearbox feeds power to the rear wheels just like in 2003.
Major work was also undertaken with the rollcage as this particular chassis featured some innovative bar work within the engine bay.
“It then went through a greater period of evolution … engine, chassis, suspension, so I needed to work back in time to basically how it rolled out of the factory when it was brand new,” Perkins said of the restoration process.
“One of the big things under the bonnet in particular is the unique rollcage system. The bar across the two shock towers comes right across the engine, the trumpets are underneath, so to get the engine in and out of the car you need to drop the crossmember and pull the engine out in an interesting manoeuvre.
“Why is this a talking point?
“We actually got rid of this after a year or two because we felt like there were more gains with a bigger airbox, more air induction, more pressure and we had to redesign all the bar work to maintain the same rigidity in the chassis without having the bar over the top.
“Placing this item of bar work back into the chassis was no mean feat and required quite a bit of effort to reinstall.
“I couldn’t restore this car and put this original airbox there knowing that this bar wasn’t there. We’ve re-engineered the car back to how it was so we had to pull out the dash, the dash in full, the firewall and re-do this to precisely how this was built.
“It’s quite a tricky thing that not many people will realise. We painted it black to try to disguise how the bar work was. The rest of the chassis is in silver.”
This was only the start as bars were removed and even the interior layout had been modified at the end of 2004 to suit the tall Davison, which has now been restored to how it was at Bathurst the year before, and much of it is hidden underneath the seat.
“In the cockpit we had to do quite a bit because the rollcage over time, without the use of CFD and engineering technology, we realised there were a few weaknesses in the strength of the rollcage,” Perkins said.
“We put a lot of bars into the car. One of the ones that’s missing, that we did take out, was an FIA driver intrusion bar we used to run on a vertical plane across the driver’s door. In the rear of the car there was a cross weld across the trailing arm boxes to really stiffen up that lower area of the rollcage.
“When the car was first rolled out, it had what we called an X exhaust system, so it had tailpipes coming out both sides, before the endurance races. In 2003 we worked out the X system wasn’t the go and the Y system where the tailpipes come out the passenger side was a better bet.
“But then, back to when we wanted to restore it to 2003, the seat was higher and the exhaust box was there so we had to re-do all that work; put the exhaust box back in, the rollcage through that section we had to re-do all that to precisely how it was in 2003. There are some little finicky parts under the seat that you’ll probably never see, but to do the job properly it needed to be done and that’s what we did, so there were no shortcuts.”
Throughout the process, Perkins discovered that due to its CAD design lineage, it was incredibly hard to work on and not very user-friendly, which as mentioned earlier was changed rather quickly.
The accuracy extends to the interior where the MoTeC gauges, the famous Perkins Engineering “tower of power” take centre stage. Perkins undertook the tough task of tracking down the exact Recaro race seat that was used for the event as the Commodore had been fitted with a VELO product.
“Tracking that exact Recaro down wasn’t easy, but Gerard McLeod had one and we were able to swap him,” Perkins told Auto Action.
“The seat had Perkins Engineering spec velcro attached to the sides for the lap belts, so the original origins of the seat may indeed have been with us, which is cool.”
The steering wheel used at Bathurst remained with the car throughout its life. It was bought from Dick Johnson Racing post-accident. The original item was bent as a result of the hit and was given to fabricator Travis Langman, who still works at Perkins Engineering on the restorations, and returned the wheel so it could stay with the car.
Many components, including the brake bias adjuster, drink bottle and TEGA monitor mounts were robbed for new car builds, so these were re-manufactured or the originals were found and the rear-view mirror was reverted to the road-going model just like in 2003.
The belts used in the accident were stretched and cut by officials. A spare pair of red MOMO belts were used at the time and reinstalled for the restoration but expired in 2008, requiring new belts for Phillip Island.
The brake system is one of the few areas of the Commodore not to be changed.
“The car was used before control brakes and rotors were introduced to the category,” said Perkins. “It started life with and subsequently finished with AP 6-piston front calipers and Brembo 4-piston rear calipers mated with AP Racing front brake rotors with ????? 01 pads and the rear set-up consists of AP Racing Rotors and Padgid RS4-4 rear pads.”
Perkins Engineering enjoyed a great relationship with suspension company Ohlins, as proved by the shaker test in 2006, so the package in the Commodore uses TT44 dampers just like it used at Bathurst 2003. It had been updated to the TTX, but was reconverted.
“During 2004, legendary race engineer Ron Tauranac came on board to assist with development,” Perkins said. “We changed to unequal length rear arms, with the lower arm being longer than the top arm. “Modifying the diff housing back to equal length arms wasn’t an easy task.”
Instead, faithfully, this Commodore has been restored to exactly how it rolled on to the grid at Bathurst all those years ago. The attention to detail is impeccable, but the car might not be in the hands of Perkins Engineering if it hadn’t “slipped through the net”.
“It’s the last car dad owned,” Perkins said. “We’ve always had the philosophy of you need to sell one to pay for the next one, so we’ve never had a car collection until after the fact. We built 49 race cars and 198 engines during 25 years of business.”
For Larry, it’s a trip down memory lane with a chassis that carries significant meaning for two generations of the Perkins family.
“A lot of good memories and a lot of bad ones with this particular car,” said LP. “I’ve never had the enthusiasm to look backwards at my old cars, so I’m very pleased and rapt Jack’s taken that on board.
“It was just a coincidence that I kept this car, it just panned out that way.
“We could easily not have kept it. To be my last race car and Jack’s first Bathurst car, I didn’t know that. It’s a real good example of what we used to do
“I’m very proud of it.”
TECH SPECS – HOLDEN VY COMMODORE V8 SUPERCAR – PE041
BODY
Holden Motorsport VY Commodore shell, Perkins Engineering designed and manufactured roll cage, chrome-moly tube, unique double main hoop roll cage
ENGINE
Perkins Engineering designed Holden Motorsport Engine – PE 184
8 cylinders, 5000cc, 625hp at 7500rpm, dry sump, M48 Motec Control ECU, Exhaust by Perkins Engineering
TRANSMISSION
Holinger H6S Gearbox with Holinger Shift Cut gear knob, control V8Supercar Gear Ratios, AP triple plate racing clutch, 9” diff, cambered diff
SUSPENSION
Front: Perkins Engineering designed and manufactured Double Wishbone Front Suspension
Rear: Cambered live-axle, multi-link, watts linkage
Ohlins TT44 Shocks, 4-way adjustable
BRAKES
AP 6 piston front, 372mm AP rotors PFC 01 pads
Brembo 4 piston rears, 372mm AP rotors, Padget RS4-4 pads
STEERING
Perkins Engineering designed and manufactured steering rack, steering column, Momo Steering Wheel
WHEELS AND TYRES
Speedline 5-spoke, Ford Offset, 17” x 10”
FUEL SYSTEM
ATL 120litre bladder, PE manufactured box, Holley Blue lift pumps, Bosch 044 High Pressure pumps, -06 hard line fuel lines with return
INTERIOR
Perkins PPG Silver paint colour, Recaro Seat, Momo 5 point harness, Perkins Engineering Designed Pedal Box, grilling master cylinders, PE throttle assembly
WEIGHT
Dry weight: 1355kgs, with LP and some BP Ultimate Petrol 1450kgs
Article originally published in Issue 1780 of Auto Action.
For Auto Action’s latest feature, pick up the latest issue of the magazine, on sale now. Also make sure you follow us on social media Facebook, Twitter, Instagram or our weekly email newsletter for all the latest updates between issues.