UNDER THE SKIN: S5000 – HOMEGROWN EVOLUTION
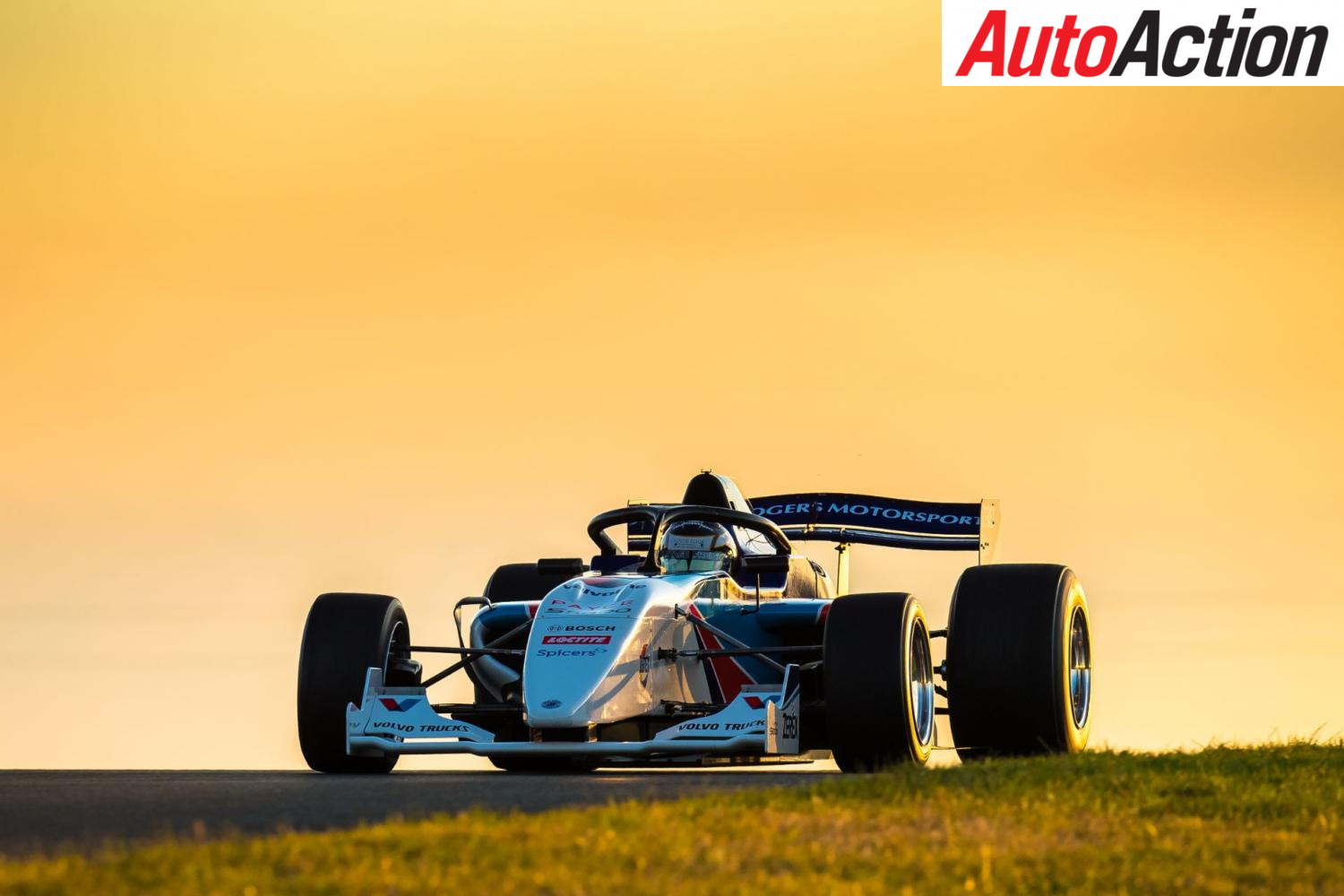
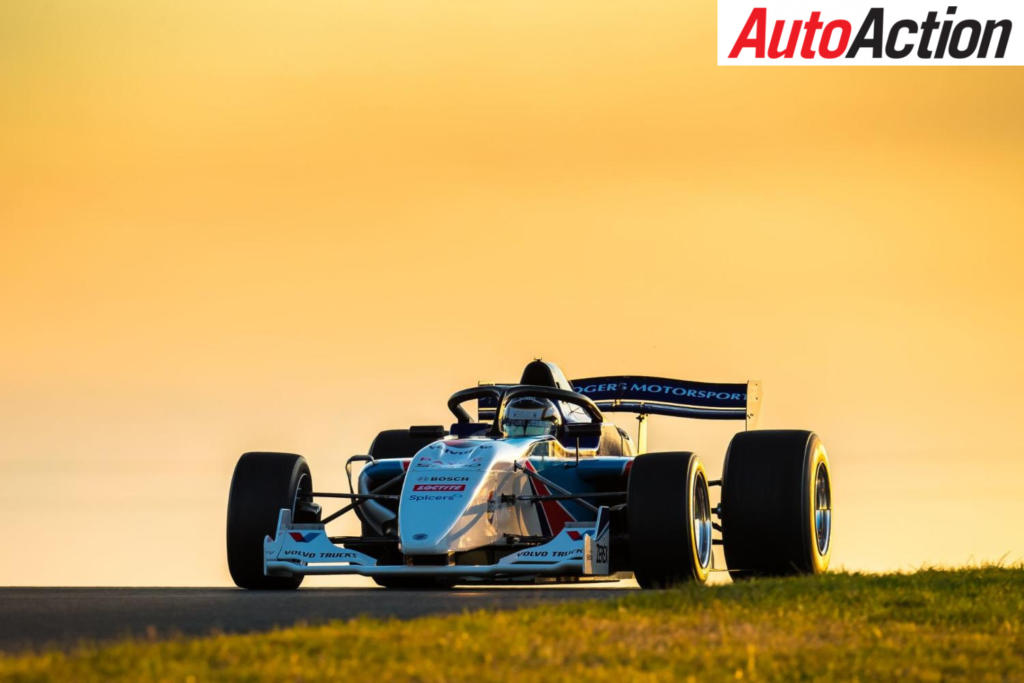
Under The Skin – S5000
Auto Action took a look at the original Swift-based Formula Thunder 5000 concept just on three years ago but things have changed and a very different car now forms the basis of the S5000 racer. Speaking with HEATH McALPINE, Garry Rogers Motorsport team manager Stefan Millard outlines the progression to S5000.
IT HAS been a whirlwind nine months since Garry Rogers Motorsport took on the responsibility of turning a prototype race car into the final production S5000.
GRM had plenty of work to do to implement the development of a production version of the S5000, after work had been kicked off by Borland Racing Developments.
Borland had undertaken the development of the original prototype of the Ligier- based car, alleviating CAMS’ concerns about chassis safety triggered by Chris Lambden’s original Swift-based FT5000 concept.
A noted-Supercars chassis constructor, GRM knew it had the workforce and the facilities to achieve the task, but the timeline was short and modifications had to be made to make the car easier to produce while at the same time staying true to the original concept of utilising Australian-made componentry as much as possible.
The first port of call for GRM was to communicate with the various suppliers before his team went through the prototype chassis to identify components that could be changed to make it more user-friendly during the assembly process.
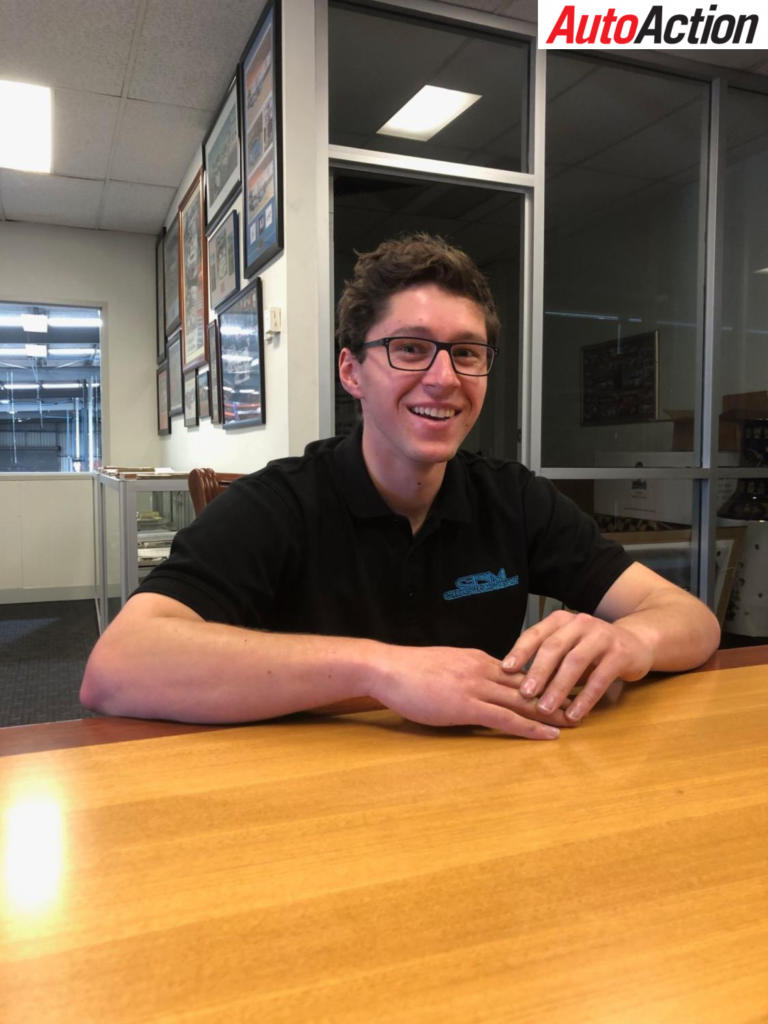
Stefan Millard
“Our first mission was to speak with all the suppliers and get an idea of where everyone was at with the project,” Millard told Auto Action.
“We obviously had the prototype there, which was the concept and the essence of what the end result was meant to be. Then from our point of view we went through it with a fine tooth comb; everything that needed to be tidied up and made into a production item was done, while keeping that original essence of the prototype car, and what the category was designed to be.”
Working with outside suppliers such as Holinger, MoTeC and Innov8 didn’t challenge Millard, as GRM has an ongoing relationship with most or had a previous relationship, enabling the team to convey what it needed for the S5000 project and set time constraints.
“A lot of the suppliers we’ve worked with in the past – the motor sport community is quite small in Australia so, at some point or another, we’ve crossed paths with many,” Millard continued.
“We had to be very clear with the suppliers in terms of what our expectations were and set some deadlines as clearly as what we could early in the project. I’d say the suppliers have done a fantastic job – they’ve put more people on when more hands on deck were needed and to meet the deadlines.”
The undertaking by GRM to complete a production run of another 13 S5000s is a rarity in Australian motor sport – normally most teams build one, maybe two cars a season, but 13? It meant that efficiency also had to be considered, which Millard identified early on during the initial construction stage.
“I’ve said it a couple of times now, for a team in Australian motor sport to build 13 cars is almost unheard of – our core business is Supercars where on a standard year teams would probably build one car, if that,” Millard explained.
“To take that mentality and then decide to build 13 of them, 14 including the prototype, we had to think about how we were actually going to get everything made in time so that the final assembly was held up as little as possible.”
Although the base chassis has been changed, one constant has been the Coyote Aluminator engine since testing first began in 2016. Since the original unit was selected, the model has undergone a couple of upgrades – especially in terms of better cylinder heads and efficiency. Power remains set at 560bhp.
Development has continued in this area with Roger Higgins from InnoV8 designing a bespoke dry sump system, individual throttle body manifold and fuel injection system for the S5000, while the billet rocker covers are also an InnoV8 product and are integral to the structure of the car, as they form a part of the mounting system between the tub and engine.
Also adding to the structural strength of the engine mounting system is a pair of exquisite struts, machined from billet, forward from the bell-housing to the rear of the tub.
“The engine starts out as a ‘crate’ motor from the US, which is a 5.2-litre Aluminator V8, the top of the line Coyote engine,” said Millard.
“Higgins combines that with the specialised parts he has evolved in his workshop where it then gets dynoed and run in for a couple of hundred kilometres. Then it gets sent down to us where we complete final fit-out with auxiliary parts such as the exhaust system, Tilton carbon clutch, air box and K&N air filter ready to put in the back of the car.”
GRM’s fabrication team led by Howard Johnson have been busy constructing the twin radiators that feature in each sidepod, using an ADRAD core and making the end tanks and hard line in-house. This is mated to a PWR bespoke oil heat exchanger.
GRM has also put meaningful time into the exhaust layout, which has been an interesting challenge as a number of considerations had to be met including packaging, cost and aesthetics.
“The biggest constraints were obviously the packaging around the engine, transmission and through the suspension arms,” Millard explained. “The exhaust itself went through a couple of iterations, which Higgins then ran on his dyno and made sure he was happy with them. It was something that was going to be mass-produced item so it had to be cost effective and easy to make in large quantities.
“It also had to be an elegant solution – something where you take the engine cover off and it looks the goods as well. The biggest thing we’ve monitored with all of them is the consistency between the cars as well – it’s a control category so we’ve put a lot of effort into our repeatability, with our manufacturing jigs, and making sure the parts are coming out the same.”
Some outsiders question the idea of significant control components, but the category’s philosophy is results based on driver skill rather than the one with the most money or best resources, so another key element to developing the S5000 was to keep it simple and keep it low-maintenance. This is carried through to the electronics, which are a MoTeC-developed system, continuing the Australian-made preferences throughout the car.
“Obviously we’re trying to really push that Australian-made technology – I think we do some pretty cool stuff in this country,” Millard enthused. “The brief from Garry was to make it as Australian as possible and MoTeC know what they’re doing.”
The MoTeC system is designed to have a minimal effect on the way the car is driven, again highlighting the skills of the driver. The desire for a paddleshift gearchange led to a lot of work being put into that part of the system, while drive by wire also features.
“There are basic driver inputs and not a whole lot else,” Millard emphasised. “There’s no traction control, no ABS, no launch control – it’s just straight up driver skill. I think a lot of people didn’t grasp that it didn’t have traction control….
“The brief from Garry was to try get the focus back on the driver rather than who has the best traction control setup and other aids.”
The bespoke wiring harness was designed in- house at GRM with the chassis and transmission sections being made by Ryan Cawley of Proloom in Melbourne and the engine harness provided by Custom Wiring and Electrical, based on the Gold Coast and headed by former Perkins Engineering crew member Chris Archer..
The involvement of Melbourne-based Holinger Engineering in Lambden’s V8 open-wheel project was a given since its infancy, with the whole rear-end of the car being designed by the company in conjunction with Michael Borland. From gearbox to differential to bell-housing, Holinger has designed a custom set-up for the S5000.
“Holinger has done a really good job – pretty much everything from the engine back is all Holinger,” Millard told Auto Action.
“Bell-housing, gearbox, differential is all custom for the S5000 and the gear set is an off-the-shelf item, but the actual castings for the case are bespoke for the S5000 and they’ve done a glorious job on it. The oil tank is integrated into the bell-housing, the catch tanks are as well, so it really makes a good package at the back of the car.
“They’ve been a good partner to have in the project.”
The Holinger MFT six-speed sequential gearbox, with reverse, features a pneumatic paddleshift gearchange with compressor. Holinger supplies a 5 1⁄2” carbon-fibre clutch from Tilton as well as the input shaft and rear axles.
A purpose-designed and built drop-gear is utilised to make sure the engine is as low as possible. Reflecting the control-spec nature of the category, gear ratios are fixed, as are the drop gears and diff settings.
“If we ever find ourselves in a position where at certain tracks we need different gearing or we find ourselves not in the window, it’s quite simple and cheap for us to just change the drop gears, which moves the whole window for the gear ratios,” Millard explained.
Ex-GRM employee Jacob Rayner of On Point Engineering has produced custom designed spindles that have been machined to match with GRM-designed uprights, which are interchangeable. As Millard says: “The upright bodies and spindles can be used on any corner of the car, which I think is going to be really good from a spares point of view and for when we start getting crash damage. Those little details make a big difference.”
A lot of the work suspension-wise had already been completed by Borland, so the S5000 retains the suspension geometry used before GRM were involved in the project. A component that has been modified slightly are the suspension arms, which were redesigned in-house at GRM with the aim of making the manufacturing process easier for mass production.
The S5000 features a traditional double wishbone and push-rod suspension set-up, a common arrangement on most open-wheelers. The twin shock, linear spring configuration utilises JRi two-way rebound adjustable shock absorbers. These are dynoed by GRM to make sure they carry the exact same set-up, while springs are an Australian King Springs item, which were made in rapid time.
“We’ve dynoed every JRi shock to make sure that they’re all the same, it’s something we don’t envision the team’s having to spend development money on and they are a sealed unit from us,” Millard explained. “The regulations limit the number of spring options, which are supplied with all the cars. Mark King has done a great job in making 180 springs in quite a short time.
“We envision when racing one of these cars – whether it be leased or purchased – that it’s just a matter of there’s the car, there’s the set-up options and you’re ready to rock and roll.”
The front and rear anti-roll bars are adjustable, but not by the driver, and the options that are supplied with the car are the ones that must be used.
Stopping power for the S5000 is provided by AP Racing, a company that has had a long association in Supercars competition, supplying the 4-pot calipers and vented rotors, which feature on all four corners of the car to again keep costs down and simplify repairs. Performance Friction brake pads are off the shelf Pf11s and are a control item.
“We wanted something that was consistent over a large temperature range and had a good modulation for the driver,” Millard added.
“Brakes are a consumable item, so it was important to keep the costs down in this area.”
The three-piece aluminium wheels for the S5000 are Australian custom-designed and constructed by MAX Wheel, headed by noted Speedway competitor and former touring car driver Max Dumesny. These will be wrapped in Hoosier control wets or slicks, 23.0×9.5R15 tyres at the front and 27.0×14.0R15 on the rear.
FIA-spec wheel tethers on all four corners of the car, a key safety feature the most visible of which is the halo. Although not a popular addition to open-wheel cars in recent years, the halo has proven its worth protecting drivers in a number of incidents since being introduced to Formula 1 last year. The halo comes supplied by Onroak- Ligier already fitted to the tub and GRM do not remove the device during assembly, which has created some minor issues.
“We haven’t worked on many open-wheelers here but the halo does provide an issue for the mechanics, because it is quite hard to work on the inside of the tub,” Millard said.
Other safety features that aren’t obvious include the FIA-spec intrusion panels and protective headrest, while the chassis has been crash tested to the latest FIA safety standards.
The fuel tank is a 62L FIA-approved ATL bladder, supplied through Onroak with a single high-pressure fuel pump feeding the engine.
The core of the car, the Onroak-Ligier JS F3 carbon-fibre chassis, is actually manufactured in Italy for Onroak-Ligier (France) and then exported to Ligier (US) in Charlotte NC where it is used, among other things, for the Formula 3 Americas series. Because of its FIA-approved safety status, modifications to the tub/safety cell itself are totally forbidden, so in order to handle and distribute the S5000 V8 loads wider, an adaptor plate was designed co-operatively by Michael Borland and Ligier US design engineer Ken Anderson, and manufactured and fitted by Ligier US before the chassis leaves for Australia.
It utilises the original rear-of-tub engine mounting points, plus some aero-quality adhesive to attach it to the rear of the tub.
The result is an integral engine mounting system in which the engine itself is a semi- stressed element, ensuring the S5000 chassis is enormously rigid and strong – just what’s required. It is an exquisite piece of engineering.
The tub itself, and the nose of the car, has undergone extensive and demanding FIA crash tests – frontal impact, rear impact, side impact.
That whole process is a long and extremely costly one – and only viable commercially for cars that will be produced in significant numbers.
It is the single reason why production of this key element of any modern single-seater race car is simply out of the question in Australia because the cost and complexity makes it virtually unviable.
Of special note, and compulsory now on all FIA-approved open-wheeler race car tubs, is an additional, virtually solid carbon plate fitted across the front of the tub, aimed at significantly increased protection for a driver’s feet. It provides a 25 percent increase in impact energy absorption, and follows on from British youngster Billy Monger’s horrendous crash into the back of another F4 car in 2017, which resulted in the amputation of the lower part of both legs.
The composites area of GRM, headed by Mick Mahendra, has been busy making the engine covers, brake ducts (front and rear) and dash panels, while the crew not far away at LC Race Composites in Mordialloc make the (modified for S5000) rear floors and rear wing, as well as the engine air box. The rest, including the front wing, comes with the chassis, from Ligier US.
Inside, the cockpit is as cosy as you would expect for an open-wheeler such as this – which means GRM had to be smart in how it fitted out the tub, installing all the key components inside.
“It hasn’t been too bad,” Millard reflected. “Carbon tubs are notoriously tight to package due to the nature of them, because each is handmade, they are all slightly different, so you have to be clever with how you do your mounting, just to accommodate the small differences in each.”
All the MoTeC electronics are fitted under the moulded seat, while Sabelt brand FIA 2016 homologated belts are supplied. Further development by GRM has gone into the steering wheel, which is custom designed, featuring a MoTeC D153 dash and shift light module. The handle grips are a custom 3D printed item, while the rest of the wheel features the paddleshifts, pit limiter, scroll, alarm acknowledge and radio buttons.
To say the S5000 features the best of Australian race car ingenuity is underselling the efforts by GRM and each of the suppliers that have been involved in the project throughout.
S5000 is world class, an excellent endorsement of what can be and is still being designed and constructed in this country.
As Millard said to Auto Action during the chat; “I think that’s the thing that a lot of people haven’t understood. People think we’ve bought a kit from the US and are just putting it together.”
That is simply not the case.
It will be a proud moment for all involved in the project when S5000 takes to the grid this weekend – and to have of the ilk of Rubens Barrichello competing is an absolute credit to everyone involved in S5000.
Let the ground shake at Sandown!
TECH SPECS: S5000
ENGINE:
Based on 5.2 litre Coyote ‘Aluminator’ V8 quad-cam engine, adapted by Brisbane company InnoV8 for S5000 – including bespoke dry sump and cam covers (both part of the engine mounting system), and InnoV8’s individual cylinder fuel injection system. Key internal parts are replaced for further strength. Fly-by-wire throttle.
Rev limit: 8000rpm
Max power/torque: 560bhp / 450ft-lbs
Flywheel: S5000 spec, by Holinger.
Clutch: Tilton 5 1⁄2”carbon-fibre.
Exhaust system: GRM designed and fabricated
Radiators: GRM made using ADRAD core, PWR engine oil heat exchanger
Fuel tank: 62L FIA approved ATL bladder. Single high-pressure fuel pump.
GEARBOX:
Holinger MFT six-speed sequential, with pneumatic ‘paddle-shift’ gearchange, features a bespoke, purpose-designed drop-gear. Gear ratios are fixed. External gearbox oil cooler (mounted between rear wing supports) manufactured by GRM. Bellhousing by Holinger, with integral oil tank, along with damper and suspension mountings. Driveline elements such as axles, input shaft are also supplied by Holinger Engineering
WHEELS AND TYRES:
Max Wheel custom designed 3-piece aluminium wheels, manufactured in Australia and supplied by MD Motorsport.
Hoosier S5000 control tyres – Front: 23.0×9.5R15 radial slick with control S5000 compound. Rear: 27.0×14.0R15 radial slick with control S5000 compound.
BRAKES:
AP vented steel rotors/four-piston 4-pot calipers on all four corners. Control brake pad: Performance Friction 11
INTERIOR:
S5000 spec by GRM with integrated MoTeC D153 dash, SLM, paddle shift, pit limit, scroll, alarm acknowledge and radio buttons. Custom designed 3D printed steering wheel handle grips, Sabelt seat belts, Tilton pedal box
ELECTRONICS:
Both engine and car systems, including dash, supplied by MoTeC. Chassis wiring loom by Proloom (Melbourne).
SUSPENSION:
Uprights, wishbones, steering arms by GRM and spindles all Australian- made.
Dampers: (2-way adjustable) by JRi (US). Adjustable front and rear anti-roll bars.
CHASSIS:
Onroak-Ligier JS F3 fully crash-tested carbon-fibre Ligier tub (safety cell), nose including front wing element and side plates, side pods, side intrusion and rear crash elements – including the ‘halo’. Includes FIA-spec intrusion panels (front and rear) and headrest, FIA-spec wheel tethers. Bespoke billet aluminium adaptor plate designed by Borland Racing Developments/Ligier, fitted to the tub by Ligier. ATL fuel bladder.
BODYWORK:
(all carbon-fibre): Engine cover, brake ducts by GRM; Rear floors, rear wing and engine airbox by LC Race Composites, Melbourne.
Article originally published in Issue 1770 of Auto Action.
For Auto Action’s latest feature, pick up the latest issue of the magazine, on sale now. Also make sure you follow us on social media Facebook, Twitter, Instagram or our weekly email newsletter for all the latest updates between issues.