UNDER THE SKIN: SUPERKART – POCKET ROCKET
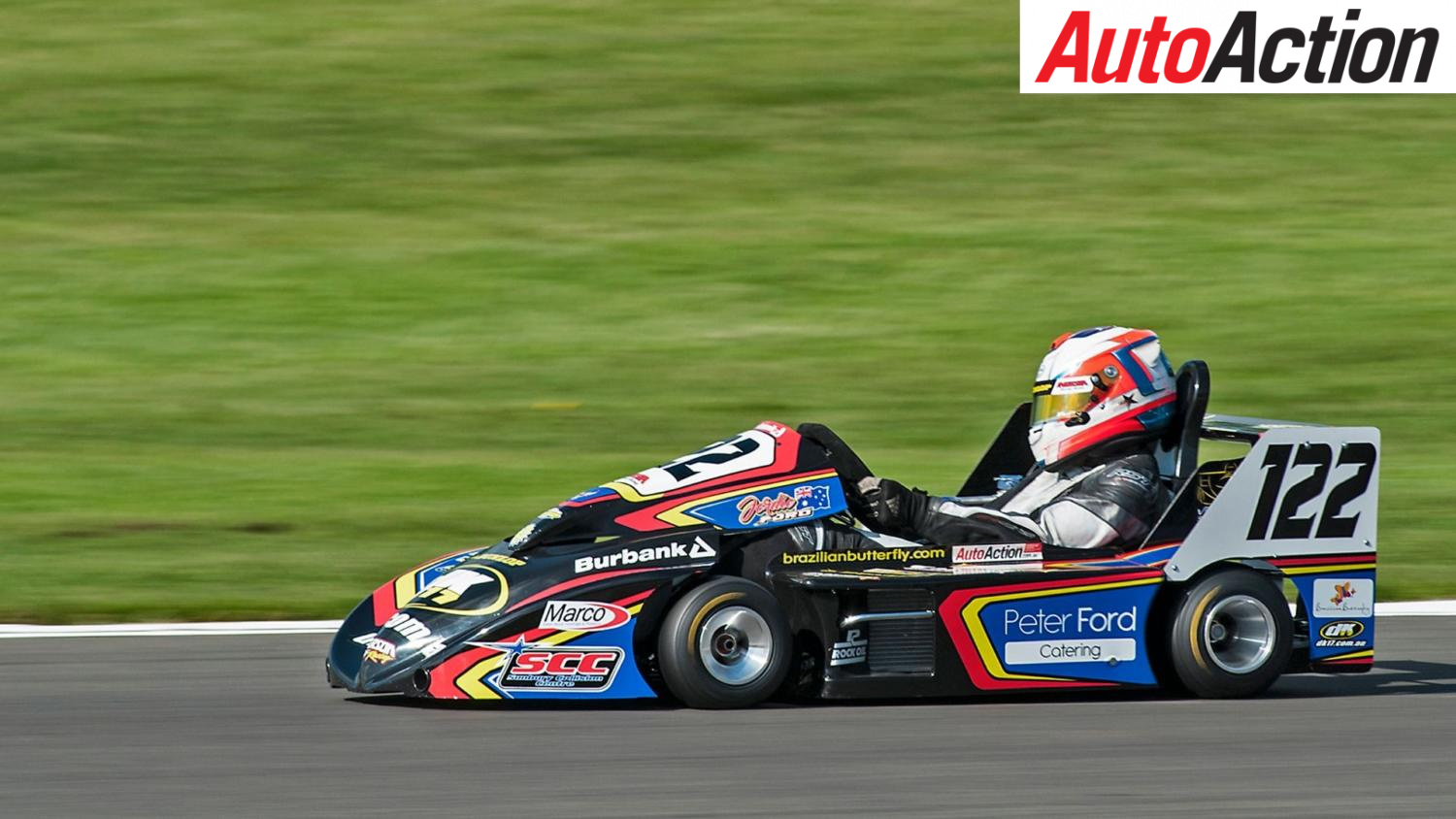
Superkart is one of the quickest types of motorsport in the world. And one of the cheapest. Not only this, but it is becoming a pathway for young drivers to experience overseas competition for the first time, or for a driver like Jordie Ford, destroy it. The Anderson chassis that took the championship is now on Australian shores and has continued its success
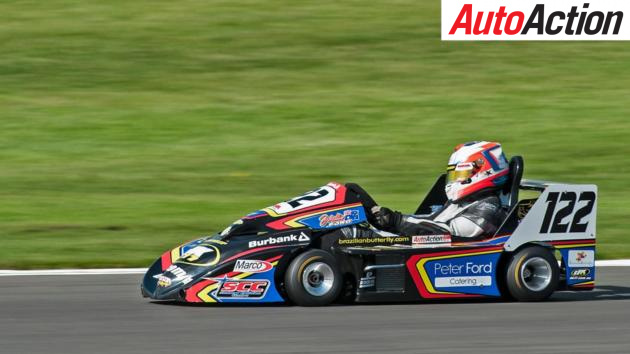
Under the Skin of a Superkart
BY HEATH MCALPINE
THE ANDERSON name is synonymous with Superkarts, the brand has taken a multitude of European and World titles in what is an extremely competitive environment. The brand was started by a Kiwi, who moved to Britain in the late 70’s after catching the bug of motorsport in his home country. Russell Anderson first started off as a mechanic for drivers such as Terry Fullerton, whose place in the sport was cemented by the comments of Ayrton Senna in the documentary of his life. Anderson soon decided that he could do things better things in the sport.
“I ended up in the UK working for Martin Hynes’s Superkart team looking after his engines and then I branched out on my own in 1984 and just went from there,” Anderson explained. “My forte was the engine tuning of the two-strokes but I branched into kart manufacturing.
“Probably about 1987 is when I really got serious about manufacturing Superkarts for championship events, so it started then and continued. We’ve had quite a bit of success since then with European and World Champions.”
Apart from Anderson’s international victories, there have been national championships in the USA, Sweden, Germany, New Zealand, Britain and here in Australia.
The developments made on Anderson’s Superkarts have been significant, namely in the chassis material, aerodynamics and engines, but the amazing thing is that despite building 30 karts a year, Anderson only has five staff and builds, designs and developments most the componentry in-house.
“We’re pretty lucky because basically, we make everything in-house, apart from the bodywork, which we have a shareholding in a separate entity that makes our bodywork,” Anderson told Auto Action.
“We own and do all the development on the moulds, but everything else is done in-house, in Yorkshire. We do all our own CNC, all our own chassis fabrication, we manufacture our brakes and all our rolling equipment, so it does give us the ability to do it virtually overnight or within a week to test.”
And there is a little bit of down under in every kart, as Anderson continues.
“The chassis, the tube is very much a black art where you get in a position to just design that. All the machine stuff is CNC. I use a program called OneCNC, which is developed in Australia. When you draw it and the NC program comes out of it, so you can actually draw it, machine everything on the computer. It prices the whole bit before you even upload it.”
Not only has computer-aided design changed the game, but advice from the top level of the sport has helped forge Anderson Karts as a consistent race winner.
“Its materials, certainly chassis materials have changed and evolved,” remarked Anderson.
“Clearly, we had quite a bit of assistance from Formula 1 guys. We had a relationship with a team and they helped us a lot, where we were going wrong they corrected us on the aero package.
“We keep trying to develop it, but a lot of it is hand and mouth, trial and error. When you make serious mistakes, you do need a bit of professional guidance to set you in the right track and even now we still get a bit of help or buy a bit of help from aero dynamists.
“The team did a bit of testing for us with our new development wing, but we did a bit of testing with it at Phillip Island, it was probably mounted a little wrong. There wasn’t a lot of time to do anything other than just bolt it on and test it. It wasn’t quite set up right, but it shows great development. We tried it in Europe back in October and it worked very, very well.”
Anderson also explained that the team helped with the design of the nosecone after his crew were encountering issues during testing, but the aero dynamists sent the Anderson crew in the right direction by ordering the team to, ‘lose this, lose that and put pressure here, there.’ Also, Anderson’s team had access to the MIRA wind tunnel (a testing facility for manufacturers in Britain) for a day, where further information was gained about the aerodynamic effects of the body.
So, what is the design philosophy that Anderson follows when designing, building and designing a new superkart?
“I’m a firm believer in not compromising in rate or lightness for reliability,” answered Anderson.
“What I really try to build into our karts is reliability, so we do probably sacrifice one or two kilos that we could lose. And in the materials, we use I am very keen that everything’s reliable and strong. That’s my key from the 90s onwards we have been renowned for having reliable karts.”
Something that is reliable is the bespoke DEA engine that was run by Ford in Europe. DE Engineering is an Italian company headed by Andrea Di Posti, a man that has developed engines with Aprilia and is highly regarded due to his perfectionism.
Anderson’s Aussie connection is Scott Williams, who is a former racer and has supported a number of drivers including Ford and ex-AFL star Jason Akermanis. Despite taking the European title last year, rule changes have meant that the Aussie clan will only contest the British Grand Prix, but Ford might be joined on the grid by a number of fellow Aussies.
Williams recently received Ford’s European title winner and was able to add further on what makes the DEA engine tick.
“It’s a specially built engine with crank case induction in the carburettor and the front exhaust exits out the back,” Williams explained.
“It runs a 40mm DEA carbie, which is the best that you can get. We ran a filter on the carbie at Phillip Island where as in Europe you have to run a special plastic CIK component. The noise pipes are restricted to 95dBa, it is very quiet compared to the other karts that compete in Australia.
“It is water-cooled and the only issues we ever have are to make sure to not get any detonations due to running on unleaded fuel. Compared to what we’re running here, in Europe your window of being in the sweet spot is a lot narrower, so we ran it rich just to play it safe. You don’t want to rev anywhere past 11,000rpm; normally you’ll rev to 10,500rpm and change to get to 10,800rpm in top gear, over a bump it might blip to 11,000.”
A five-speed gearbox drives the rear wheels by regulation, with Ford using a lever on his left-hand side to change gears due to his previous experience.
Maintenance on the engine is relatively straightforward, with piston and ring being the one part to look out for, but generally both last two to three meetings, as do brakes, while the Dunlop tyres last two meetings. The tyres have been specially developed for Australia’s warmer conditions, therefore the durability is much better than the European equivalents.
Another option the is specific to Australian teams is also due to the much hotter conditions that are a feature down under as Williams pointed out.
“In Australia we generally have to run another radiator in the back, but because Europe is a lot colder it isn’t necessary. At Phillip Island [in early February] it was just borderline whether we needed to put a second radiator on it because the cooling is very good compared to the Yamaha engines we run here. Again, it is an option, but during winter we will run one because it weighs 5-6kg to run the second one, plus because it is mounted on the back it creates a bit of drag.”
The seat in the superkart is as centred as possible alongside the engine and Williams assured that the driver feels every bump, while the steering wheel in front includes most of the electronics, which features all the important information that Ford requires while he is driving.
“We run a Mychron system, which we can run up to two sensors, so it runs a water temperature sensor, a tacho, GPS,” Williams told Auto Action.
“We can run an exhaust gas temperature, but because these engines don’t have a balance shaft it tends to vibrate a bit, so it actually breaks the sensors out of the pipes and we did away with it because of the fatigue. And as Russell says “what driver is going to slow down if the exhausts getting too hot?”
Not only that, but the Mychron system also collects useful data that can be applied to a wide range of circuits across the world.
“We can do sector times and overlay data and one of the more interesting things was when we were competing at Donington, from the Yamaha engine we ran here to the engine we had over there, we went from Sydney Motorsport Park to Donington the next week and same gearing, maximum top speed and same RPM. It was interesting to see the similar characteristics between the two.”
The brakes are an important factor of the car and one in, which Anderson continue to develop. The brakes featured on Ford’s superkart are disc brakes with four-pot at the front and six-pot at the rear, each is an Anderson factory product.
“We’re running the oversized bigger discs that they run on a 250 twin, which is an option,” said Williams.
“We certainly didn’t get outbraked anywhere last year, it’s all hydraulic and built in house by Anderson. It’s called a five-star braking system, we run a hard compound pad, which pulls it up well as the braking distances are between 100m-50m into the corners. To go from 239kmh into a chicane style corner it does pull up very quick.”
The body is fibreglass, although carbon fibre is an option, but for is not required due to Ford being rather slender. In fact, the team had to install lead weights in Europe to make the minimum weight, so it was determined the carbon fibre wasn’t worth the outlay, which saves up to $3500.
The fibreglass bodywork design is interesting as it features a number of hidden grooves and diffusers, which guides the air through the body and through a number of vents to cool the brakes and the side-mounted radiator.
“There is a bit more work underneath at the front, it does have some ducts like a semi-diffuser, which gets the air away and includes the brake ducts,” Williams continued.
“On the rear there is a diffuser as well, there isn’t a lot of room, there isn’t a lot of aerodynamics on the bottom, but just before the axle line to the back there is a diffuser. The rear wing is what Anderson call its low drag wing, which is basically flat.
“When it got crashed into at Assen, it broke off the end plates, so side stability wasn’t quite good, but he still managed to break the lap record six times in a row.”
What about set-up? The car has stayed reasonably the same since arriving in mid-January, with Anderson’s quoted set-ups working perfectly at a Phillip Island in early February, with the only adjustments being the height of the nosecone and dialling out some understeer. If more time was given Anderson could have tinkered further.
“That’s really about being on top of the engine tune and I noticed that the wind changed up and we had a tailwind halfway through the day [at Phillip Island],” Anderson said.
“Performance-wise you want to keep on top of that and quicker guys probably do, they know if the winds giving them a bit of a push down the straight. They probably want to increase their gear ratio and air pressure developed. If I was coming back I would be looking at all those things.”
“Like all motorsport, I think it’s all about getting the feedback from the driver.”
‘So, what is in the future for Anderson Karts? Improved aero is still a key area that Anderson hopes to improve on and the constant evolution of different foundries in Europe has also aided in chassis design.
“Rear wing is an area we are concentrating on at the moment, we’ve concentrated on bigger front brakes in the last couple of years, which has added to the performance.
Really, we’re just looking at a bit of aero at the moment, not much in chassis design. We may go to different rear axle diameter and material to one some more valve and weight. We haven’t done any running with that yet, but with the new rear wing design and that’s really where it is just refining what we have got.”
“We don’t do big leaps and bounds into unknown areas.”
TECH SPECS – ANDERSON MAVERICK 250 NATIONAL SUPERKART
Engine DEA single cylinder engine
40mm DEA carburettor, DEA exhaust, twin radiators (in hot conditions)
Power 72hp
Chassis Anderson designed chrome-moly chassis
Gearbox: Anderson five-speed
Cockpit Quick release fibreglass seat, Mychron steering wheel. The Mychron system has attached gauges that provide tacho, water temperature sensor and GPS, while also collating data.
Brakes Adjustable brake bias
F: Anderson developed four-piston calipers, 162x12mm rotors
R: Anderson developed six-piston calipers, 200x12mm rotors
Fuel Tank 13lt
Dimensions Length: 2108mm Wheelbase: 1099mm Width: 1100mm Weight: 212kg
Bodywork A choice of Carbon Fibre or Fibreglass body panels featuring front and rear diffusers, rear wing and side pods.
Wheels and Tyres Australian developed Dunlop 6” tyres
Article originally published in Issue 1730 of Auto Action.
For our latest Under The Skin feature pick up the current issue of Auto Action Magazine, on sale now. In the meantime follow us on social media Facebook, Twitter, Instagram or sign up for our weekly email newsletter for all the latest updates.