UNDER THE SKIN: HAYWARD 014 – RUNNING UP THAT HILL
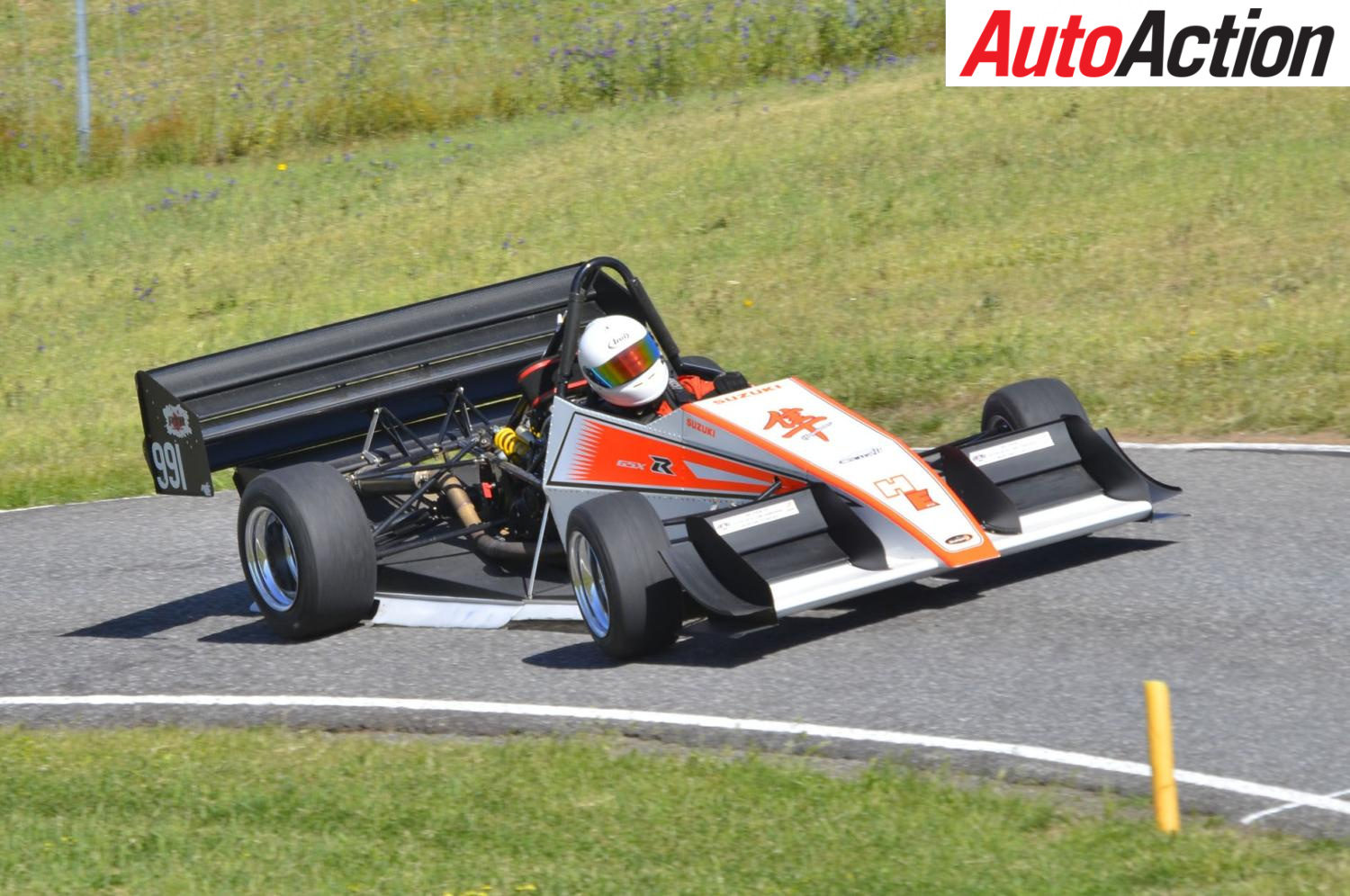
Brett Hayward is a three-time Australian Hillclimb Champion and won this year’s in a car that he built four years ago from scratch. The Hayward 014 is a marvel in engineering and shows the high level of competition shown in a discipline forgotten by some – but not by the men and women in the Hills
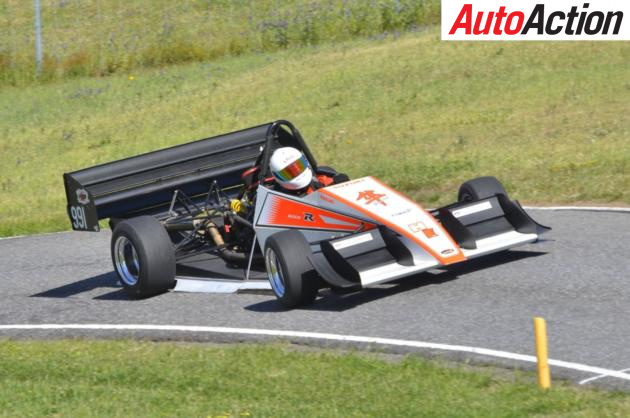
Under the skin of the Australian Hillclimb Championship Hayward 014
WHEN MANY fans think of hillclimbing, they think of older gentlemen wearing tweed jackets, smoking cigars and watching older British sports cars struggling to climb up rather steep hills, but that it is quite the opposite.
Read further on and discover that these cars are well advanced compared to many race cars in Australia, and yes, the car was built in a backyard shed, but Brett Hayward has engineered a super quick and strong race car out of a hobby he discovered 20 years ago after deciding to head back to four wheels from two due to injuries.
“I grew up on a dairy farm up in Gippsland and from the age of 14 or 15 I started building my own karts using a motor out of an old bike, welded the frame up and it just evolved from there,” explained Hayward.
“I got into motorbikes when I was 18 or 19 I got into riding and racing dirt bikes, and over a period of time I kept falling off and breaking bones, so I thought it may be best to go back to four wheels. I run my own engineering business in Leongatha and when I started that I think I still had a dirt bike and I thought it was silly because if I hurt myself I can’t run the business, so ended up selling the bike and built some autocross buggies.”
Hayward started out building Honda Odyssey Buggies before building his own chassis and it progressively got more serious, including the manufacture of three to four four-wheel-drive versions until he went to the old Morwell hillclimb. This was when he decided to move his attention to building his first purpose-built hillclimb car, ‘The Ninja’.
“I raced that car for a couple of years and it was quite quick and successful – I won a couple of 1300 Australian Championships in that car,” Hayward remembered fondly. “It had a standard 1300cc motorbike engine, but was also competitive in the outright scene, I only raced in Victoria back then. I thought that was really good and I could do one better because I was smarter after watching the other competitors.
“After ‘The Ninja’ was built in 1999, which was followed by a new car in 2003 and a new car approximately 18 months thereafter. What happened was I’d race the car for 18 months and come up with better ideas that made the car faster.”
The 2007 season was a milestone for Hayward as he built his first customer car, and by 2009 he had built his first championship winning car, the Hayward 09, which took out the title at his home climb at Bryant Park in the Victorian Gippsland region. This car was raced competitively for four years before his current 014 was built.
The decision to build his latest creation came as the competition lifted, especially with Malcolm Oastler’s British-built, but self-developed OMS, Greg Ackland’s Ackland GA8 and Tim Edmondson’s Gould GR55B Nicholson McLaren took the honours in the following years. As this was going on he was also building a seriously quick four-wheel-drive hillclimb car for the Race To The Sky event in New Zealand, which returned in 2015 after a 10-year hiatus.
After taking his new design to most of Australia’s top hillclimb venues, he had targeted a third title the 2017 Australian Hillclimb Championships at Collingrove in South Australia as his main aim for the year. However, a mountain bike accident in late 2016 left him in a brace for five months left him underprepared for the event, but much to his and especially his competitors surprise he won.
How did Hayward do it? First of all, the car is a rather simple machine and requires limited set-up for different climbs, mainly based on the surface. Secondly, Hayward has kept the common theme of using trustworthy materials and components that he can rely upon to take the surprising amount of stresses a hillclimb car goes through. Finally, he has learnt from each model that he has built and improved it dramatically from the previous incarnation.
The improvements have not been over one particular area of the car, but have been made in each area, some more significant than others, though each has an important impact on the car. Surprisingly, however, no Computer Aided Design (CAD) worked has been used in the design of this bespoke vehicle.
“It’s a bit crude as far as that goes,” Hayward admitted about the chassis design. “I have a jig bench and I’ve never used any computer-aided design, it’s all just been using what I have learnt from the last car you’ve built. It’s just a matter of incorporating more bracing for strength and rigidity.
“I use chrome-moly, but originally we used mild-steel tubing, which is no lighter, but we can use half the material for the same [amount of] strength, which makes the car lighter.
“In the design it is more triangulated, I’ve done something quite unique in the rear of the car, my engine and drive chain for the rear differential are actually on a five-six-degree angle from the chassis centre line. It’s purely for design to keep the chassis skinny at the back, it’s like a big triangle just to save weight. I have to have longer wishbones, but wishbones are made out of lighter material than what the chassis is.
“The chassis are a lot lighter and stronger than the old days because we have gotten a lot clever now with how we build the chassis, these days we try and make the crossmember do a multitude of tasks rather than just a crossmember that mounts around the bar to mount your battery I try and use every bit that’s there for a reason not to just hold together. We use a lot of aluminium bars and chrome-moly tube for the bracing through the floor. I look back at my old cars and think, ‘what was I thinking?”
How weight is placed in the car is also crucial to how fast the 014 handles, but Hayward and his rivals have discovered that front-end grip is very important, which has led to plenty of experimentation has been applied to the driver’s seating position and engine placement.
“Ideally, we are trying to balance the weight front to rear and with this car, with me in it has a 56-44 split. How we do that is because we run a motorcycle engine, which is light and we just build everything as light as we can and move all the weight forward.”
An uprated engine from a Suzuki Hayabusa motorcycle powers Hayward, mainly thanks to its lightness, but also due to the accessibility of aftermarket modifications.
“We’re allowed to do anything you like [to the engine], so you have classes of 1300cc or 1300 to 2-litre. The biggest you can take it to is 1640cc, which is what I have done. All of the components, most we get out of America from APE, which do a lot of aftermarket motorcycle stuff for the drags and for circuit racing cars like Radicals. It’s basically a supermarket for bike hot up parts, so you can buy a lot of stuff off the shelf. I get a place in Melbourne, Phil Paton Racing, who has been involved with Superbike racing for years and he builds my engines for me. I supply the components and do the homework, while he does the porting and the heads. The engine is highly modified and runs a stroker crank, big bore and piston, fully ported head and high-performance camshafts.
“It’s a really good engine and they are so popular worldwide in cars of all sorts now,” Hayward told Auto Action. “It’s an 80kg engine package with a six-speed sequential gearbox. Back in the day, to be competitive you needed a big V8 or a supercharged car engine, but then as we worked out a lot of the tracks suit the lighter cars. We are still maybe half the horsepower of some of the higher horsepower cars, but at the end of the day if the car is still 100kg lighter it wins out most times at most tracks.”
Aero is another development that Hayward has found significant gains after he accepted an invitation he couldn’t pass up.
“I was invited to Monash University and I spent half a day in its wind tunnel, which was an eye-opener for me and what was discovered was that we didn’t have enough aero in the earlier models.
This has been a major improvement thanks to new wings that have been supplied from the UK and the addition of aero through the floor and a rear diffuser. The floor is made from aircraft-grade aluminium, which is expensive, but has the characteristics that Haywood is after – strength and lightness.
The gearbox is a standard Hayabusa six-speed sequential unit, which is train driven and uses an aluminium rear sprocket for weight.
“The gearbox is quite standard, I just have to dog-cut first and second gear for the dog exchange because they tend to jump out under high load and install heavier clutch springs, so the gearbox is very bulletproof on the car,” said Hayward.
The inclusion of motorcycle parts is prevalent throughout the 014 due to the advancement in motorcycle technology compared to a car as the competition between the major manufacturers ensures advancements are made much sooner than in the car industry. Parts are also of better quality and lighter coping with the rough surfaces and sudden dips that make up a hillclimb.
Hayward uses Yamaha suspension components, but also hand makes some of the other suspension components while using ingenious ideas to get the maximum from his creation.
“I use Yamaha coil over shock absorbers because we have found that they don’t wear out and get better use of the off-road type, years ago we did use dirt bike shock absorbers. We stick to road bike stuff that we source from the wreckers, which are good, it’s a compression, rebound spring adjustment and we design a rocker assembly for each inbound shock to work with the weight of our car, so instead of getting springs made we can adjust the ratio of the rocker and the ride height through the push rods.”
Hayward has also used other open-wheel cars as inspiration and takes ideas that could potentially continue the rapid development of the 014.
“We’ve always gone to the inboard suspension and all that, but I have also gone to a lot of [race] meetings. I looked at Formula Ford and there were some parts that I said, ‘that’s pretty good’ and then there were other parts that were on Formula Holdens and a lot on Historics. I looked at a lot from different eras and used all the things practical that I thought would work and incorporated all that together, plus I looked other successful hillclimb cars and looked at the most cost-effective options.”
As impressive as this car is, the time spent building the car proves Hayward’s devotion to winning. Despite stepping back in recent year’s due to a growing family, Hayward spent a remarkable amount of hours on the 014 thanks to the intricate handmade components that are a major feature.
“The 014 car I have now was probably a 600 hour build on the car whereas the earlier cars were 300 hours,” Hayward explained. “But for those [early cars] we were using a lot of car components for instance hubs, uprights, rear uprights. Though modified but in essence there were no car components light enough that could handle the load, so we have to hand make all those parts; for example, axles.”
And how about the bulletproof reliability? Yes, it is aided by the limited hours the engine runs, but in the chase for pure lightness some competitors push the envelope too far when it comes to suspension components and the like. This is a risk that Hayward isn’t keen to take.
“My cars have been pretty much bulletproof over the journey,” concluded Hayward. “Over the years I have built a car, bolted it together, put it in the trailer, taken it over, raced it at a hillclimb and won outright. Rivals are like, ‘you haven’t even tested it,’ and I say ‘but I have built six cars before and I’d be embarrassed if it came out of the truck and didn’t work.’
“I have mucked a round with suspension for a little bit and changed ride heights and stuff like that, but we’ve never really had to go back to the drawing board. It maybe a little over-engineered, but that’s what comes with being an engineer for a living preparing agricultural equipment, I am a little bit paranoid about things failing, I’d rather have it a little heavier and strong. I have seen a lot of guy’s build hillclimb cars over the years and try to save weight, but they become quite fragile.
“There are some parts that I have been reluctant to make light like driveshafts, rear uprights and equipment that has a bit of load.”
The stereotype of the tweed jackets and MGs are blown into the weeds when it comes to modern hillclimb cars, which has to be one of the most interesting and highest developed classes in the country.
“I can build what I want to go racing, I can get on the track and have a real hot go.”
By HEATH McALPINE
Article originally published in Issue 1727 of Auto Action.
For our latest Under The Skin feature pick up the current issue of Auto Action Magazine, on sale now. In the meantime follow us on social media Facebook, Twitter, Instagram or sign up for our weekly email newsletter for all the latest updates.