Under the Skin: Toyota 86
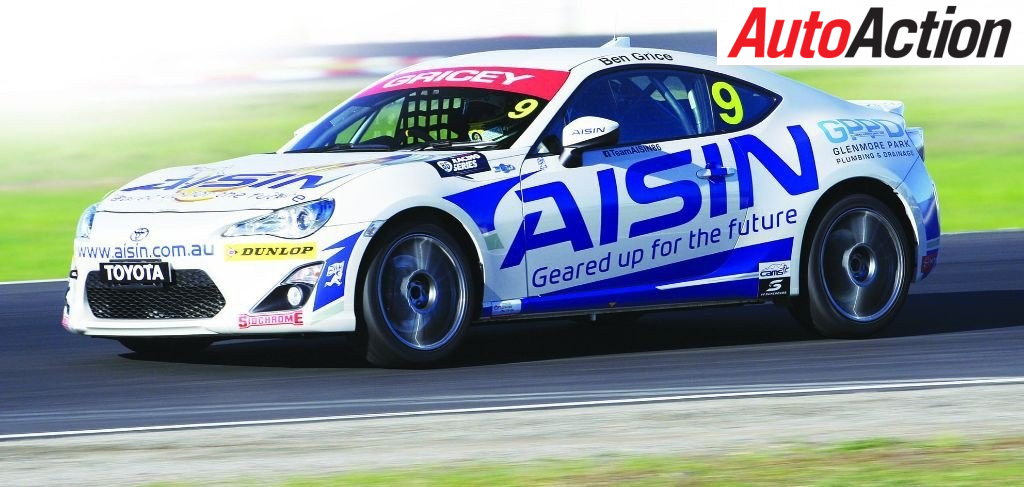
Toyota 86: A Recipe For The Racetrack. What does it take to prepare a showroom queen to a black top blaster?
You do not have to look far to see that the Toyota 86 Racing Series has been one of the success stories of motorsport in Australia in 2016 and will continue to at least 2026 to make It a decade old.
The opening round at Winton Motor Raceway in May was packed with entries and there are more cars being built around the country.
The five-round series, which concludes at Homebush in December, has provided the opportunity for drivers from far and wide to show their skills, and has attracted drivers from 17 to well, not quite 70.
Drivers range from teenagers straight from karting to veterans of the sport like Production Car stalwart Garry Holt – whose age is probably best described as “experienced”.
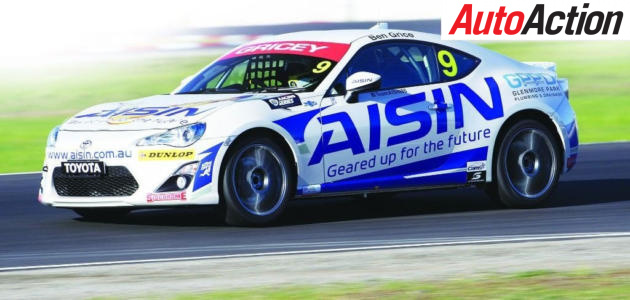
Ben Grice racing in the Toyota 86 Series back in 2016 at Winton.
At the heart of the series is Toyota’s 86, in GT and GTS model variants, which first appeared on the Australian market in 2012.
The car, jointly developed by Toyota and Subaru, has been hailed as the successor to iconic Japanese cars such as Toyota’s 2000GT and Celica, and Nissan’s 240Z, and has been a big hit with customers and customisers right around the world.
It did not take long for people to start thinking of it as an ideal racing car and that is where the one-make series came in.
Long-time Toyota consultant Neil Crompton started to talk to Toyota’s Mike Breen some time in 2014 and from there, momentum grew.
Along the way there were some important targets that had to be met. The series had to have a ‘Hollywood’ aspect by appearing on some of the country’s biggest stages, to ensure that there was an opportunity for entrants to attract sponsors, as well as giving
Toyota the exposure to justify what is far from a cheap exercise. Once that box was ticked – and the support of what was then known as V8 Supercars was pivotal in that process – it was full steam ahead.
The next step was to introduce a technical aspect to develop the cars. Enter Neal Bates, whose record of achievement needs little introduction to anyone reading this magazine. Bates set to work, carefully at first, to figure out what he needed.
“What I wanted to see was something that was exciting, relatively cheap to run and hopefully not a ‘slot car’, something that’s not over gripped,” says Bates.
“I chose a treaded tyre, which some people may not like, but for me, if you had slicks, it would become an over gripped car that you would just hold flat everywhere. You want people to have to drive them.”
That was a pivotal choice. The similar series in New Zealand, for instance, runs on a racing slick.
The other major difference between the two series on opposite sides of the Tasman is that our Kiwi ‘cuzzins’ source their cars from a common supplier.
“They don’t have an ECU that’s locked and the difference is, over there that they are built by one person and over here we are allowing people to build their own so it should be more cost effective for them,” says Bates.
“When you are putting it in other people’s hands, you have to control things a bit tighter as well, but it’s pretty easy to control things when you’re building all the cars.
“There’s several kids running and with their father they built the car, which is fantastic. But if you didn’t have control parts or control rules, you’d have 38 different cars out there.”
With costs under control – the aim was to make the price of a ‘kit’ to build an 86 into a racing car cost $20,000 – Bates wanted to cement parity into the equation.
“The biggest thing we wanted was parity, so hence the MoTec ECU,” he explains.
“People think it’s there for power but it’s not; it’s there for parity because, when you have standard ECUs, people can get into them [and] reflash them in minutes.
“They [MoTec] hadn’t developed the M150 for the car as yet. They actually borrowed our very first development car, to actually do the wiring for that car, but it was something they were doing anyway.
“They saw that as a car that people were going to play with and needed an ECU, so they were doing it anyway.”
The Toyota 86 regulations have been developed with driver safety as one of the key factors.
The homologated roll cage has been carefully designed to make the car very safe in a high speed crash situation.
While Neal Bates Motorsport has developed the cage and has supplied many of the cars racing, other roll cage builders are permitted to fit the control spec cages. This car features an Advanced Vehicle Design manufactured cage, built to the control specifications
Suspension and tyres were high on the list of items.
“We wanted suspension that was going to make them a bit more ‘racy’ and have a bit better handling,” Bates said.
“You would jump into a road-going 86 and say the brakes are fine, but put 38 of them on a track on a 40 degree day and they won’t do the job.
“Also, the GT and GTS have different-sized brakes as a standard car, and Toyota didn’t want to discriminate on which model.
“Therefore a brake package allowed everyone to have the same brakes, and something that wasn’t going to run out of brakes.”
AP came to the party as brake supplier and competitors who have driven the standard car and Series racers back-to-back leave you in no doubt about the measure of the improvements to the track car. Wheels and tyres?
“It’s an OZ wheel,” says Bates.
“Once again, when you are dealing with a company like Toyota on this, they want to make sure everything is going to be strong and reliable, and the standard wheel is obviously very strong and reliable. But like any car, you go and buy a standard wheel, they’re expensive.
“It’s also part of the aesthetics, to look better with an 18-inch wheel. Obviously it looks a bit smarter. Also because it’s a treaded tyre, an 18 gives you a bit more tyre, which lasts a bit longer as well.”
Safety is always high on the list of anyone involved in category management and this is where there were absolutely no corners cut by Bates and his team.
“Initially Toyota wanted to do a CAMS approved rollcage, but the problem is, when you go to tracks like Bathurst, the first thing you talk about is safety.
“A standard cage could be a six-point, bolt-in cage, which if you’re doing 220 kilometres per hour at Bathurst with 38 cars out there, it’s probably not particularly safe.
“The other thing was, with the standardised car, you’d use the same chassis stiffness for everyone.
“If you have different cages and chassis stiffness is different, you look at people at the front, for instance, and say, ‘that cage must be better because they’re beating us’ – and then you have people cutting cages out, redoing them and trying to find the best [cage design]. This design stops any of that happening.”
Dunlop supplies the Series’ control tyres and already there has been a slight modification to the tyre regulations, which is meant to close any slight crack in the door that could lead to slight advantages being gained at significant cost.
“Since round one the tyre rule has been revisited,” Bates explains, “because we didn’t have the [rule] that the tyres had to come from the track – the supplier at the track – which doesn’t give an opportunity for people to heat treat or tamper with tyres. Now it’s four tyres, from [bought at] the track. There are things like that that evolve and change.
“There was conversation at Winton that people were heat treating tyres. Whether they were or not, and quite possibly they weren’t, this new rule stops that.
(Neil) Crompton’s been around for a while, I’ve been round for a while and you want to be sure that the person who wins at the end is the best driver.”
At the first race in the series there were 38 entries and the racing was strong up and down the field.
“We would have been happy if there was mid to high 20s but obviously 38 exceeded everyone’s expectations,” says Bates.
“When you’re at Winton and you see 38 going out the pit gate it seems like they’re never going to stop going out. That was a pretty amazing sight to see them out on the track.”
“It was rewarding to stand at the end of the pit lane there at Winton and see the cars roll out,” Crompton continued.
“We have a whole bunch of competitors from right across the sport, and it was great to see.”
None of this has come about accidentally. More than 2100km of testing was undertaken at seven different venues, to get a wide range of differing conditions and track surfaces, so that there were few, if any, surprises at the first event.
“I think the racing was very, very even at Winton and you couldn’t see anyone having a big advantage, or anything,” Bates said.
“I think we’ll need to get a bit of running at tracks like Sandown and Bathurst before we know that 100 percent, but I would say the times in qualifying and the race were incredibly close.”
The other side of the equation is how the competitors received the class – which, obviously, was with some enthusiasm. One of the entrants is long-time racer and car owner (and yes, the Publisher of AA) Bruce Williams, whose AISIN-sponsored car is raced by Ben Grice.
“From the point of view of a customer, it’s a good package,” Williams says.
“It’s been developed with the thought that the first time racer/car builder could put the car together themselves.
“Everything is made to fit and complement existing components in the car, and I like the fact that they have gone for quality components that may have cost a little bit more than some of the cheaper options.
“But in the long run, the quality of the parts will actually make the cars more affordable to run.
“While the cars are not overly powerful, the limited modifications that have been permitted, in combination with the chassis/brake/tyre package, give the car overall good lap speed.
“Once the cars are sorted, they don’t really need a lot of tuning, and they are not labour-intensive at the track, which helps to reduce the cost to competitors.
“The biggest job is fitting the cage into the car, that is a pretty substantial item. Given the high-speed nature of some of the tracks, such as Bathurst, and the varying levels of experience among the drivers in the category, it’s an important safety feature.
“I think that the total build time would be in the order of 120 to 140 hours for the whole car and around half to two-thirds of that was the time it took to put in the cage.
“The durability of the cars looks to be one of the best features of the car. Running costs are pretty low and the cars with the most kilometres on them seem to go better than the ones with less!
“Apart from some electronic issues, which many teams have had, the cars themselves are pretty bulletproof.”
The proof of any series’ success is in how many competitors vote with their feet – and wallets.
With more cars being built there could be nearly 50 entries by the time the Toyota 86s take to Mount Panorama in October which, by any measure, marks the series as a runaway success.
And those involved with its success are not resting on their laurels, with Bates scoring the efforts to far as eight out of 10.
“If you looked at numbers for competitors that’s a 10 out of 10, but I’m always a believer in everything can always be better, so it can never be a 10 out of 10.
“But I’d say it’s going reasonably well – and it can certainly get better.”
Listen to Supercars star David Reynolds in the latest edition of the AUTO ACTION RevLimiter Podcast HERE
Auto Action, Australia’s independent voice of motorsport.
Listen to our latest podcast episode on your podcast app of choice or here on Apple Podcasts.
For more of the latest motorsport news, pick up the latest issue of AUTO ACTION